Design of Hot Runner Injection Mold for Large Data Storage Box
Analysis of Plastic Component
The dimensions of the large data storage box product are shown in Figure 1, with a maximum overall size of 370mm x 289.27mm x 250mm. It is made of ABS material with a shrinkage rate of 1.006 and weighs 1194 grams. The average thickness of the plastic component at the gate is 4.0mm. The plastic component has a rectangular box shape, with one side being taller and inverted, requiring the design of a large slide.
As an exterior component, the plastic part should not have any defects. The challenge in mold design lies in the large size of the plastic component, which requires a large mold. For large molds, the strength and rigidity of the mold are crucial. Excessive strength would result in significant waste, while inadequate strength would lead to irreparable losses.
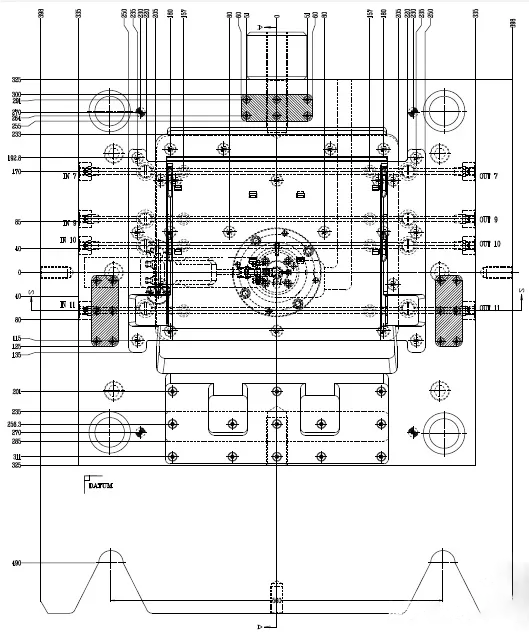
Key Points in Mold Design
1. Mold Positioning
The large data storage box product belongs to the large-scale production of plastic products. Due to the large size of the product, the mold is arranged in a one-to-one manner. The mold cavity is a non-standard 6765, and the precision frame, slider groove, and ejector pin slot of the mold are opened at the mold cavity factory to ensure processing accuracy. To ensure the rigidity of the mold frame, positioning pins are added between each mold plate on the mold cavity.
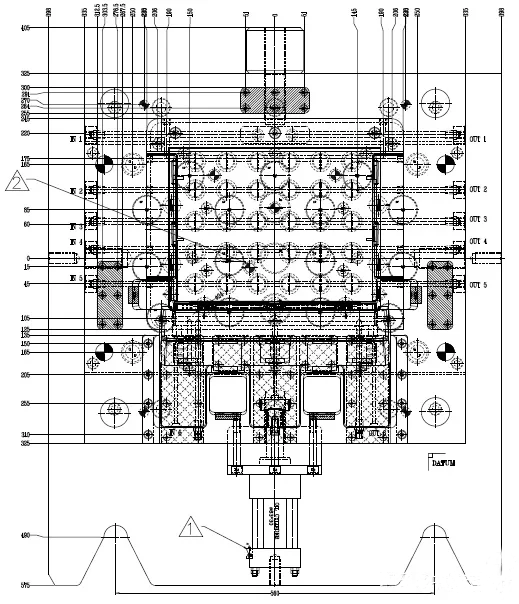
2. Injection Method
The plastic part has a large size and thick wall thickness, with multiple ribs on the slider, resulting in a longer process. The mold uses MOLDMASTER brand valve gate hot runner system, with a single-point hot nozzle.
The significant characteristic of an open hot runner nozzle is its smooth melt flow channel that does not cause flow branching. Depending on the material being processed, there may be gate marks on the plastic part, which can affect its appearance. Due to the simple design of open hot runner nozzles and relatively easy mold processing, they are widely used due to their lower pressure loss and good filling performance.
The sealing and freezing of valve gate gates is achieved through the mechanical action of the valve pin (hydraulic driving mechanism, mechanical driving mechanism, or compression spring, etc.). The valve gate hot runner nozzle effectively solves the problems of flow hesitation or stringing that occur when using open hot runner nozzles or hot tip hot runner nozzles. Moreover, the gate marks are smooth, and there is a wider selection range for gate diameters. With larger gate sizes, its injection process is more versatile and easier to adjust.
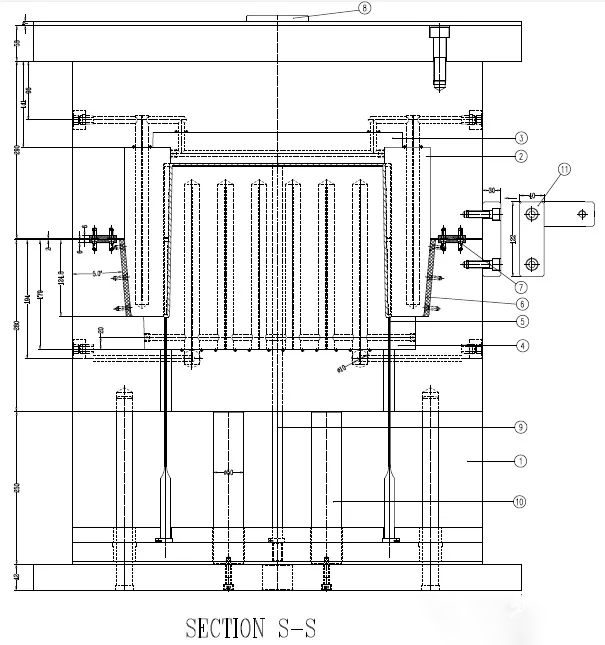
3. Design of Positioning and Guiding Mechanisms
In this case of a large injection mold, due to the non-closed design of the plastic part, the cavity and slider bear significant lateral forces. Relying solely on guide pillars and bushings for guidance is not sufficient to counteract these lateral forces. The front mold core assembly (see Figure 6) has poor rigidity, so it is necessary to add a taper positioning mechanism that allows the higher portions on both sides of the front mold core to extend into the rear mold plate. The addition of a wear-resistant plate 6 effectively addresses the issue of insufficient rigidity. Three spacer plates 7 are designed around the cavity to balance the mold locking force.
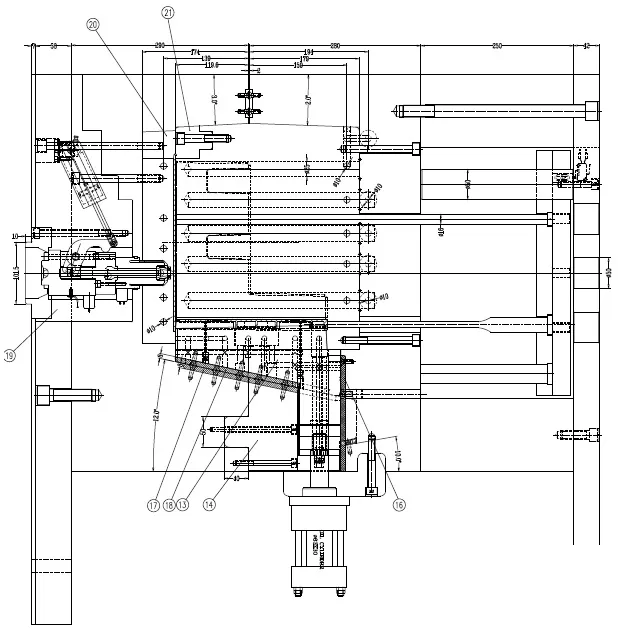
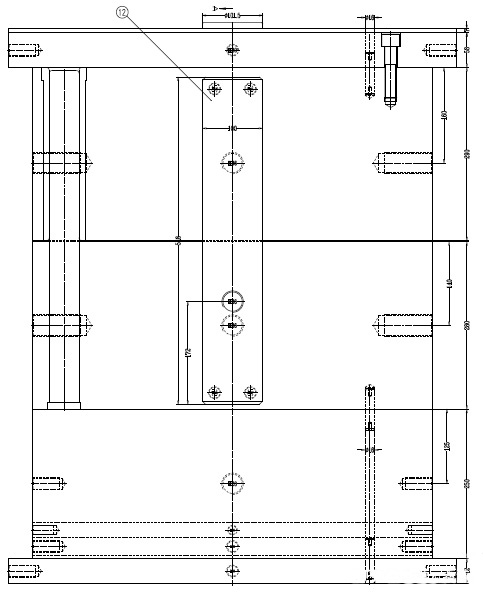
4. Mold Interlocks
The injection molding machine used for the plastic parts is an NB520-ton machine, which is commonly used in the UK. The front and rear molds have interlocking slots for safe and reliable mold interlocking.
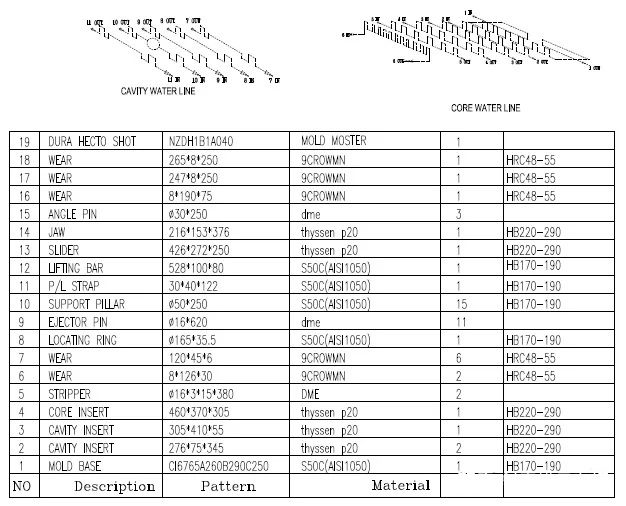
5. Ejection Mechanism Design
The ejection of the plastic parts is achieved using ejector pins and flat ejector pins.
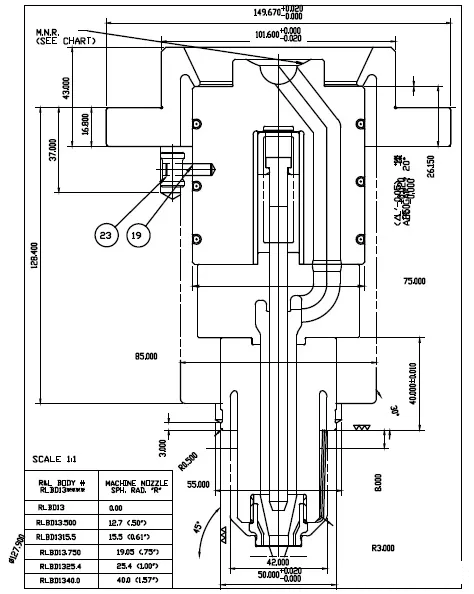
6. Lateral Core-Pulling Mechanism
The slider is driven by hydraulic cylinders. The slider (see Figure 4) has multiple ribs, and manufacturing it as a whole would result in poor venting and require extensive EDM processing. Therefore, the slider is divided into two inserts (see Figure 8), and the ribs on the inserts can be ground down. To facilitate grinding, the dimensions are indicated with an inclined annotation.
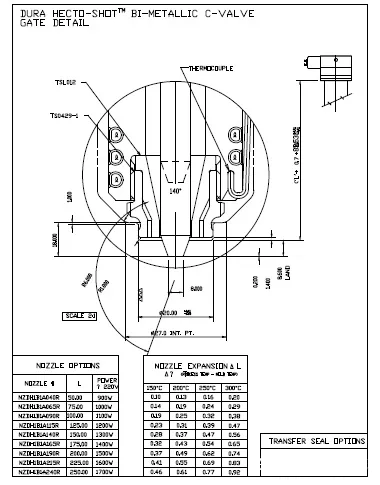
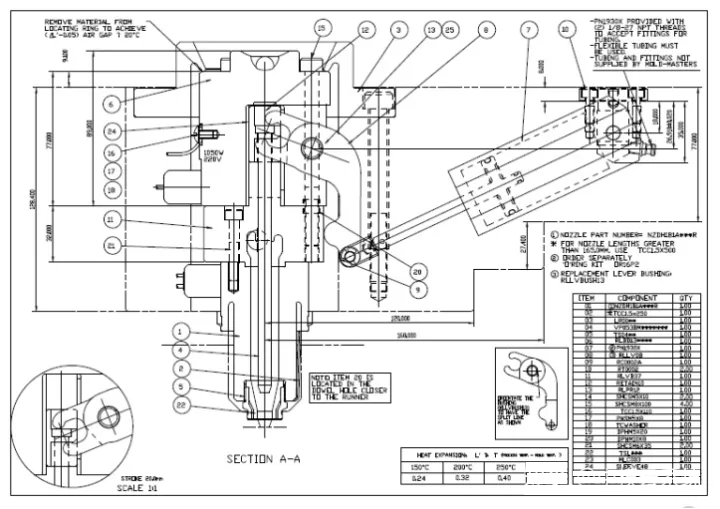
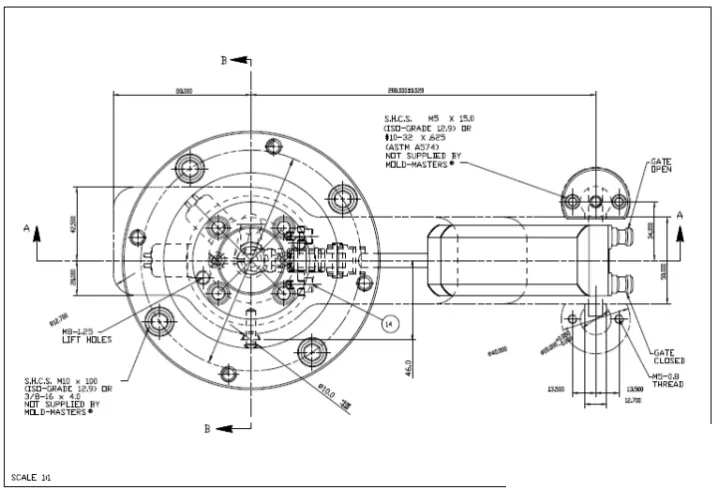
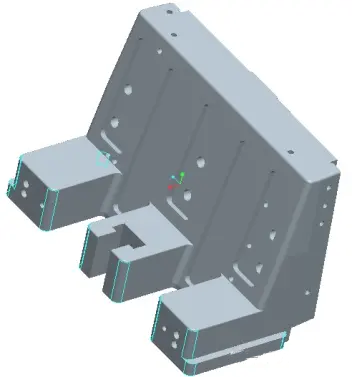
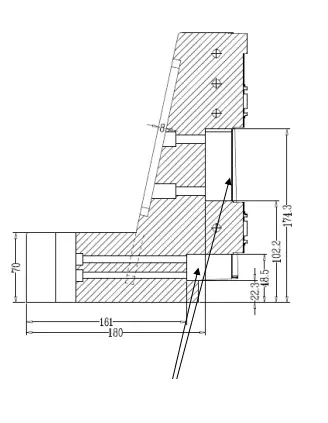
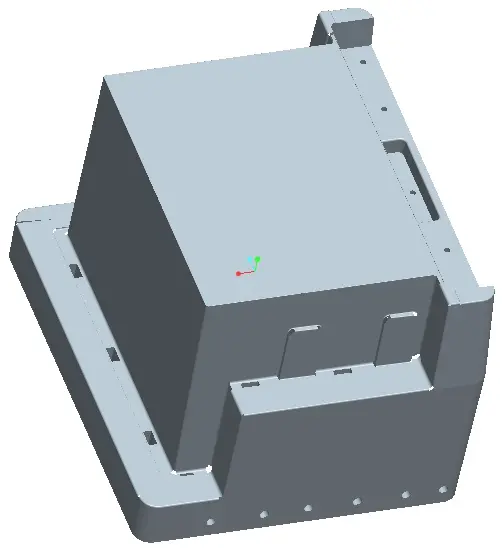
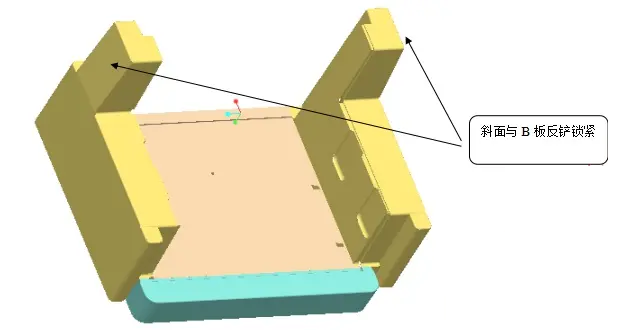
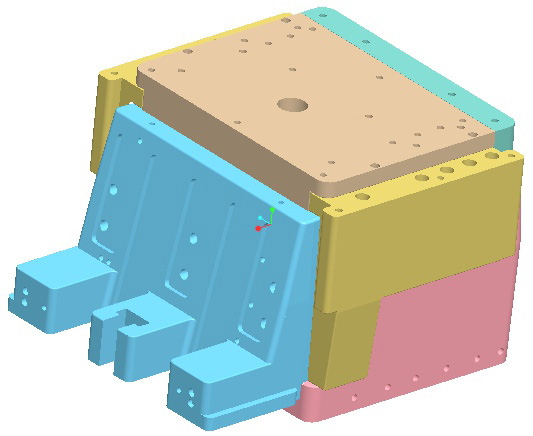
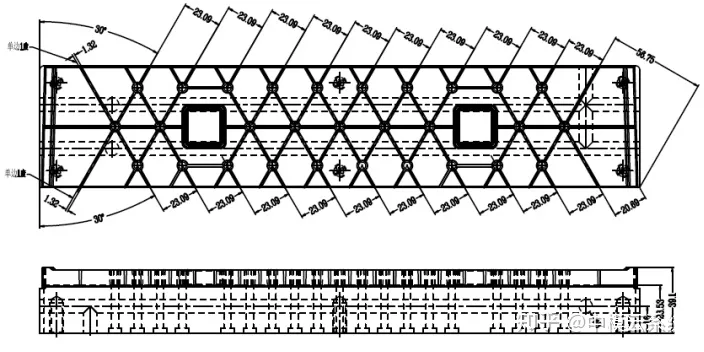
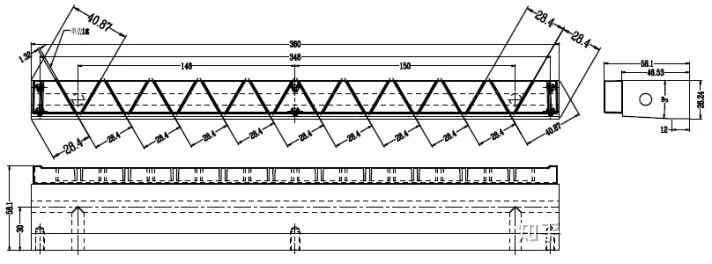
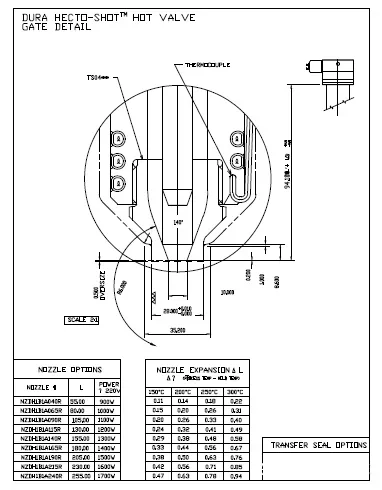
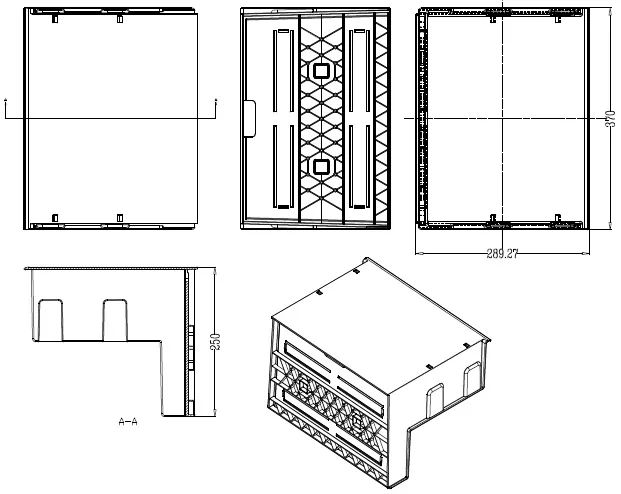