Understanding the differences between aluminum 6061 vs 6063 is crucial for successful CNC machining projects. Aluminum alloys 6061 and 6063, both part of the 6000 series, exhibit distinct differences in strength, machinability, extrudability, heat treatment response, surface finish, and applications, making them suitable for a wide range of CNC machining and manufacturing needs.
While 6061 aluminum stands out for its superior strength, machinability, and post-extrusion performance in structural applications, 6063 excels in extrudability, corrosion resistance, and achieving finer surface finishes, making it ideal for architectural and decorative uses.
Key Differences Between 6061 and 6063 Aluminum
When comparing aluminum alloy 6061 vs 6063 for precision machining, manufacturers must understand their unique characteristics. The key differences between 6061 and 6063 aluminum affect various aspects of CNC aluminum machining, from tool selection to final surface finish.
Common Applications in Aluminum Machining
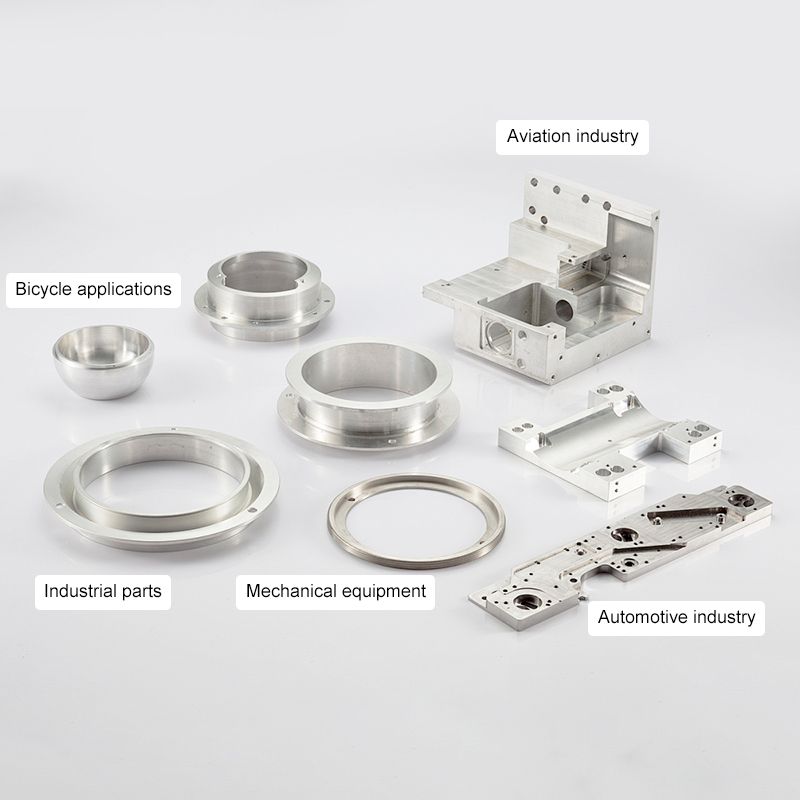
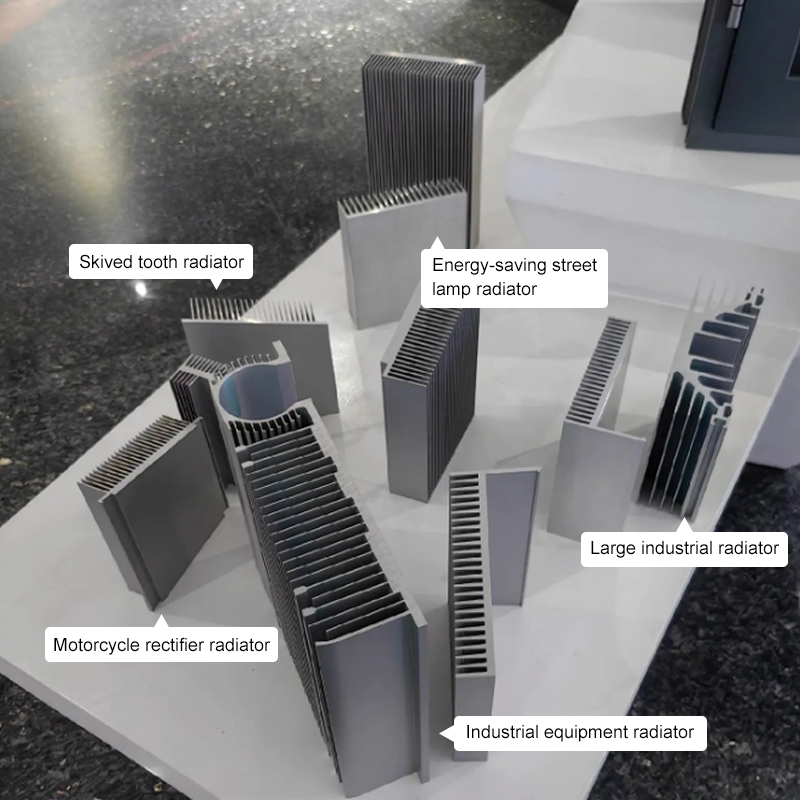
6061 and 6063 aluminum alloys serve distinct roles in various industries due to their unique properties. 6061 aluminum is primarily used in structural applications requiring high strength, such as aircraft components (wings, fuselages), automotive parts (chassis, suspension), and marine equipment. Its superior machinability and strength make it ideal for CNC-machined parts in aerospace and defense industries.
Conversely, 6063 excels in architectural and decorative applications due to its excellent extrudability and surface finish. It's commonly used for window frames, door frames, railings, and other architectural elements. 6063 also finds applications in electrical conduits, irrigation systems, and furniture due to its corrosion resistance and formability. While both alloys are used in the transportation sector, 6061 is preferred for structural components, whereas 6063 is often chosen for decorative trim and roof rails.
Strength Comparison in CNC Applications
When comparing 6061 and 6063 aluminum alloys for CNC applications, strength characteristics play a crucial role in determining their suitability for specific machining tasks. The following table summarizes key strength properties of these alloys in their T6 temper, which is commonly used in CNC machining:
Property | 6061-T6 | 6063-T6 |
---|---|---|
Ultimate Tensile Strength | 310 MPa (45 ksi) | 241 MPa (35 ksi) |
Yield Strength | 276 MPa (40 ksi) | 214 MPa (31 ksi) |
Shear Strength | 207 MPa (30 ksi) | 152 MPa (22 ksi) |
Fatigue Strength | 97 MPa (14 ksi) | 69 MPa (10 ksi) |
Brinell Hardness | 95 HB | 73 HB |
6061-T6 aluminum consistently demonstrates superior strength properties compared to 6063-T6, making it more suitable for CNC applications requiring higher structural integrity. The higher strength of 6061 allows for more aggressive cutting parameters in CNC machining, potentially reducing machining time and improving overall efficiency. However, the lower strength of 6063 can be advantageous in applications where easier formability or a smoother surface finish is desired, such as in decorative or architectural components.
Aluminum Machining Characteristics: 6061 vs 6063
In CNC machining, 6061 aluminum generally outperforms 6063 in terms of machinability. The higher silicon content in 6061 (0.4-0.8% vs 0.2-0.6% in 6063) contributes to its superior chip formation and tool life. 6061's higher strength also allows for more aggressive cutting parameters, potentially reducing machining time. However, 6063 excels in extrudability and surface finish, making it preferable for applications requiring complex profiles or aesthetic appeal.
Key differences include:


-
•
Aluminum 6061 resists "mushing" or clogging of cutting tools better than 6063
-
•
6061 allows for higher cutting speeds with lower tool wear
-
•
6063 may require more careful parameter selection to avoid deformation during machining
-
•
Heat treatment significantly impacts machinability, with T6 temper generally providing better results for both alloys
6061 vs 6063 Extruded Aluminum
Aluminum alloys 6061 and 6063 exhibit distinct characteristics in extrusion applications, influencing their suitability for various manufacturing processes. The following table compares key properties relevant to extrusion:
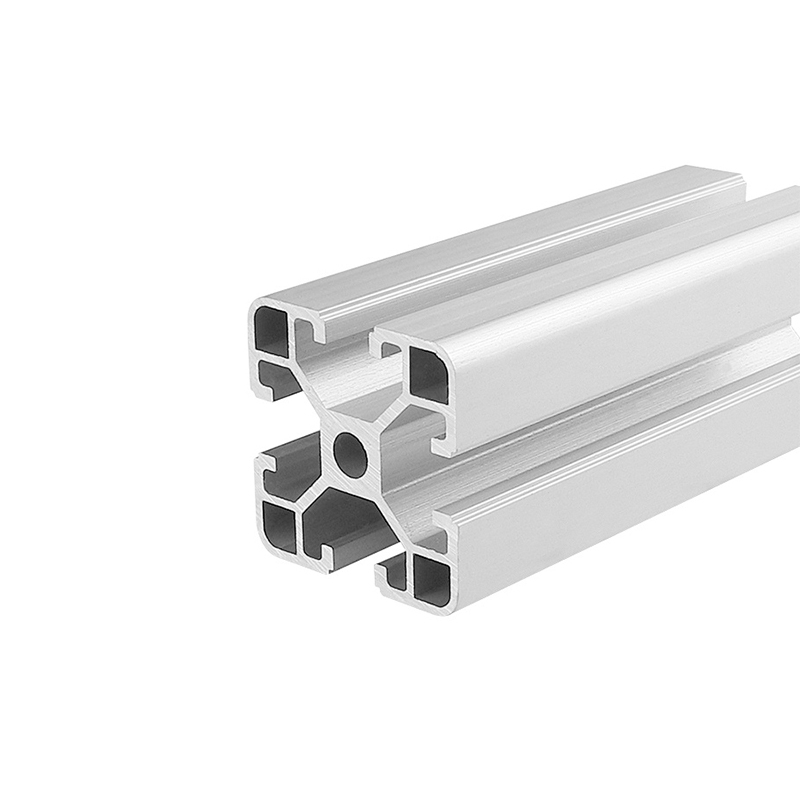
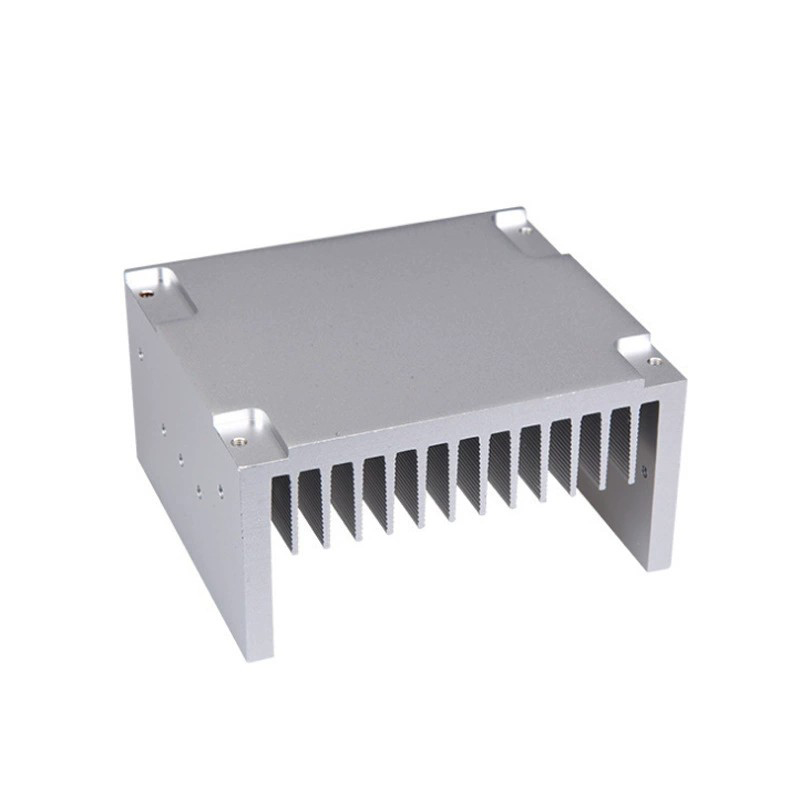
Property | 6061 | 6063 |
---|---|---|
Extrudability | Good | Excellent |
Extrusion Speed | Moderate | High |
Complex Profile Capability | Moderate | High |
Post-Extrusion Strength | Higher | Lower |
Corrosion Resistance | Good | Excellent |
6063 aluminum is generally preferred for extrusion processes due to its superior extrudability, stemming from its lower silicon content compared to 6061 aluminum alloy. This characteristic allows for higher extrusion speeds and the creation of more complex profiles, making 6063 aluminum alloy ideal for architectural and decorative applications.
However, 6061 offers higher strength post-extrusion, making it more suitable for structural applications where mechanical properties are critical. Additionally, 6063 exhibits better corrosion resistance, making it a preferred choice for applications exposed to weather or water. The choice between these alloys for extrusion ultimately depends on the specific requirements of the end product, balancing factors such as profile complexity, strength needs, and environmental exposure.
Impact of Heat Treatment
Heat treatment significantly influences the properties of 6061 and 6063 aluminum alloys, with 6061 generally exhibiting a greater response to thermal processing. The T6 temper, involving solution heat treatment followed by artificial aging, is commonly applied to both alloys. For 6061-T6, this process typically results in a 30% increase in fatigue stress and a 50% improvement in hardness compared to its annealed state.
Key differences in heat treatment response include:
-
•
6061 achieves higher strength and hardness post-treatment (Brinell Hardness of 95 vs 73 for 6063-T6)
-
•
6061 exhibits a greater deformation coefficient after heat treatment
-
•
6063 maintains better thermal conductivity (200 W/m-K vs 170 W/m-K for 6061-T6)
-
•
Heat treatment can eliminate micro-segregations in both alloys, improving overall mechanical properties
-
•
The precipitation hardening process in 6061 is more pronounced due to its higher copper and magnesium content
These heat treatment characteristics significantly impact the alloys' performance in CNC machining, affecting factors such as tool wear, cutting parameters, and final part properties.
Surface Finish Considerations
Surface finish plays a crucial role in CNC machining of aluminum alloys 6061 and 6063, affecting both functionality and aesthetics. For 6061 aluminum, which is harder and more abrasion-resistant, achieving a smooth finish typically requires more aggressive machining parameters or additional finishing processes. In contrast, 6063's softer nature allows for easier attainment of finer surface finishes, making it preferable for applications where appearance is paramount.
Key considerations for surface finish in CNC machining of these alloys include:
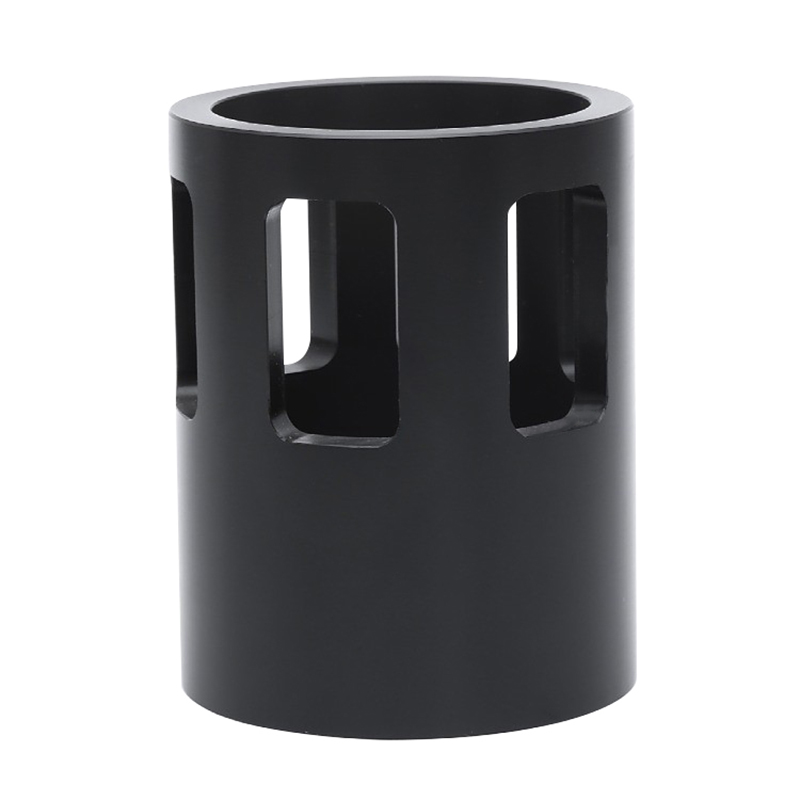
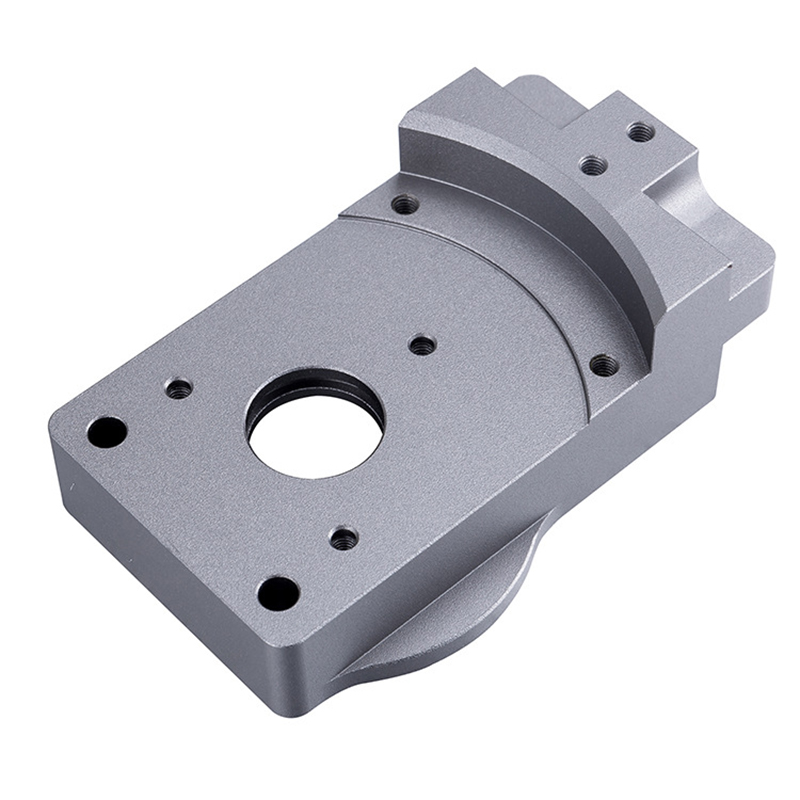
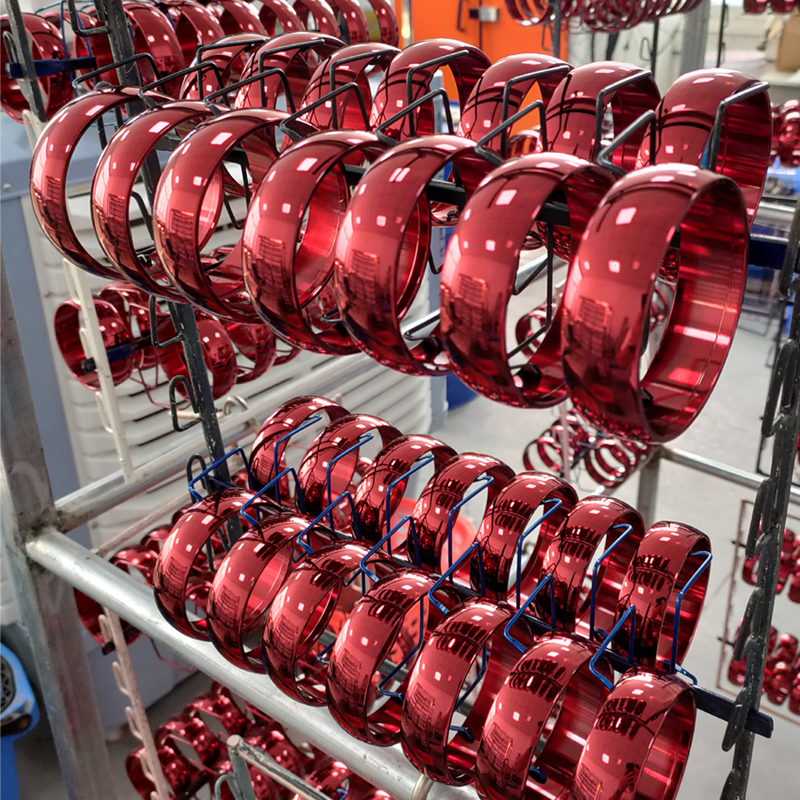
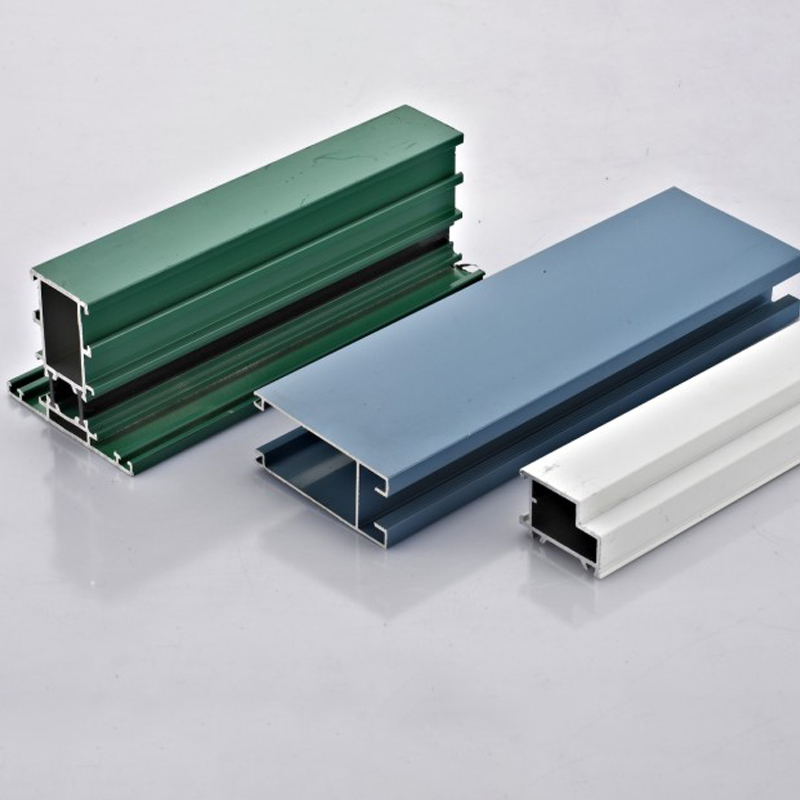
-
•
Ra (Roughness Average) values: aluminum 6063 generally achieves lower Ra values more easily than 6061
-
•
Isotropic vs. anisotropic finishes: 6063 tends to produce more uniform, isotropic surfaces
-
•
Impact on subsequent processes: Smoother finishes may not always be ideal for painting or powder coating
-
•
Machining parameters: Slower feed rates and higher spindle speeds typically yield smoother finishes for both alloys
-
•
Tool selection: Carbide tools with specific geometries can enhance surface finish quality in both 6061 and 6063
Conclusion: Choosing Between 6061 and 6063 Aluminum
When selecting between aluminum 6061 and 6063 for CNC machining projects, consider these key factors:
- Strength Requirements: Choose 6061 for high-strength structural applications
- Surface Finish: Select 6063 for superior aesthetics and anodizing results
- Machining Complexity: 6061 offers better chip formation and dimensional stability
- Extrusion Needs: 6063 excels in complex profile formation and extrusion speed
- Environmental Factors: 6063 provides slightly better corrosion resistance
- Cost Considerations: 6063 is typically more economical than 6061
Both alloys offer excellent machinability, but understanding their distinct properties ensures optimal material selection for your specific CNC machining requirements.
Need Expert Advice on Aluminum CNC Machining?
Our team of specialists can help you select the right aluminum alloy for your specific project requirements.
Get a Free ConsultationFrequently Asked Questions
What is the main difference between aluminum 6061 and 6063?
The main difference lies in their composition and strength. 6061 has higher strength and is better for structural applications, while 6063 offers better surface finish and is ideal for decorative applications.
Which is better for CNC machining, 6061 or 6063 aluminum?
6061 is generally preferred for CNC machining due to its better machinability and higher strength. It maintains better dimensional stability during machining and produces more consistent results.
Is 6063 aluminum cheaper than 6061?
Yes, 6063 aluminum is typically slightly cheaper than 6061. This is because 6063 requires less alloying elements and is primarily used for extrusion applications.
Can 6063 aluminum be used for structural applications?
While 6063 can be used for light structural applications, it's not recommended for heavy-duty structural use due to its lower strength compared to 6061. It's better suited for architectural and decorative applications.
Which aluminum grade has better corrosion resistance?
Both 6061 and 6063 offer good corrosion resistance, but 6063 generally has slightly better corrosion resistance due to its higher magnesium content and cleaner surface finish.