Fluid Control: The Advantages of C45 Steel Valve Body Connectors
In modern industrial settings, fluid control is paramount, and valve body connectors play a crucial role in ensuring efficient management of fluids across various applications. These connectors are essential for reliable operation in environments characterized by high pressure and elevated temperatures. This article explores the advantages of using C45 steel in valve body connectors, delves into the intricate manufacturing processes involved, and highlights their performance metrics and diverse applications in industries such as petrochemicals and pharmaceuticals. Understanding the significance of fluid control systems and the role of valve body connectors sets the foundation for appreciating their impact on industrial efficiency.
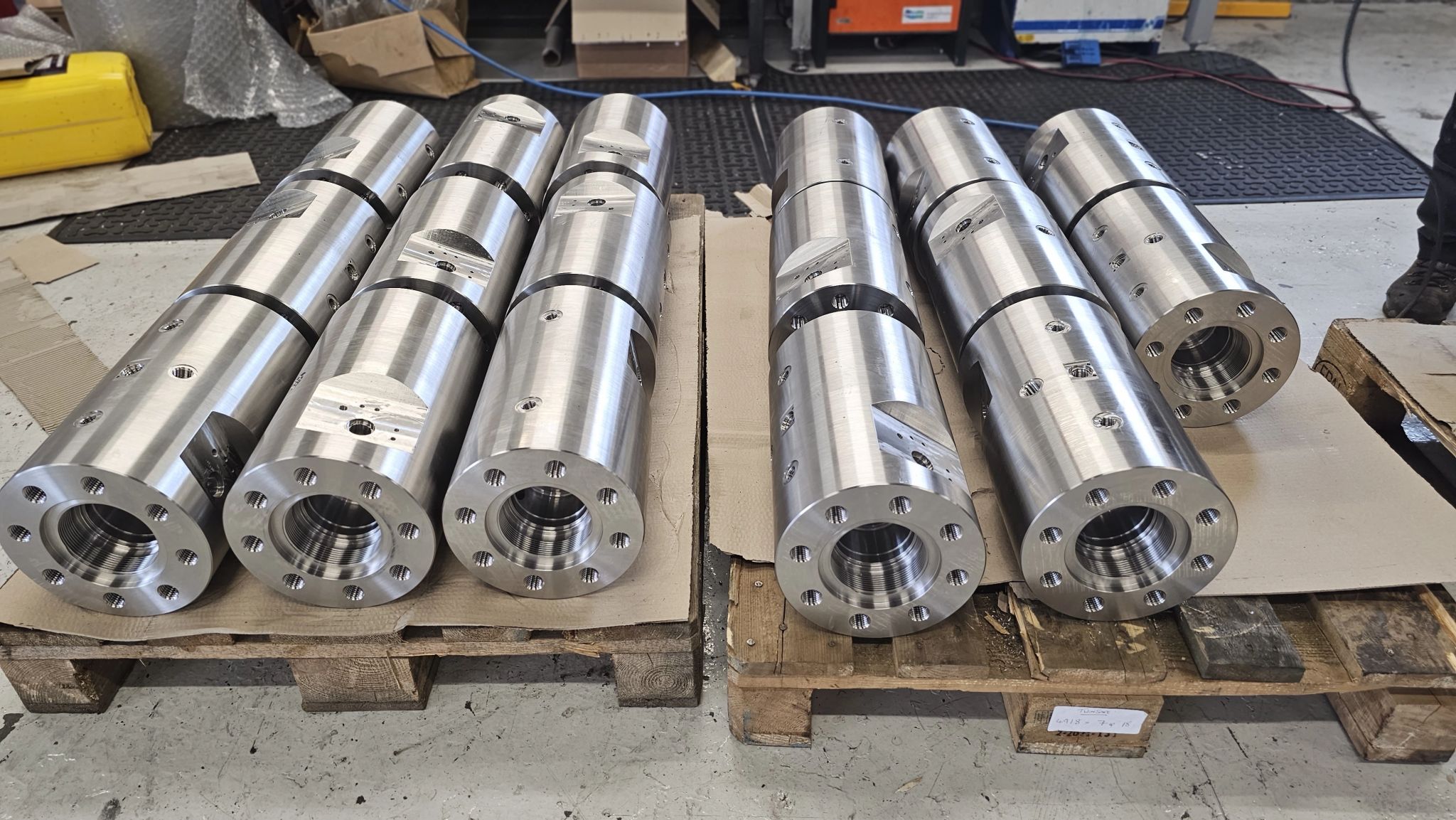
Material Selection: The Superiority of C45 Steel in Fluid Control
The choice of material significantly affects the performance and longevity of valve body connectors within fluid control systems. We often turn to C45 steel, known for its medium carbon content and exceptional mechanical properties. This steel offers a balance of strength, ductility, and wear resistance, making it ideal for high-stress applications in fluid management.
C45 steel’s corrosion resistance enhances its suitability for industrial fluid control, particularly in harsh environments where reliability is critical. The ease of machining this material allows for flexible manufacturing processes, ensuring that connectors can be produced with high precision to meet specific operational needs.
Moreover, the mechanical properties of C45 steel ensure that these connectors maintain their integrity under pressure, which is vital for ensuring leak-proof valve systems. By selecting C45 steel for our valve body connectors, we optimize their lifespan and reliability, making them a preferred choice in various fluid control applications across multiple industries.
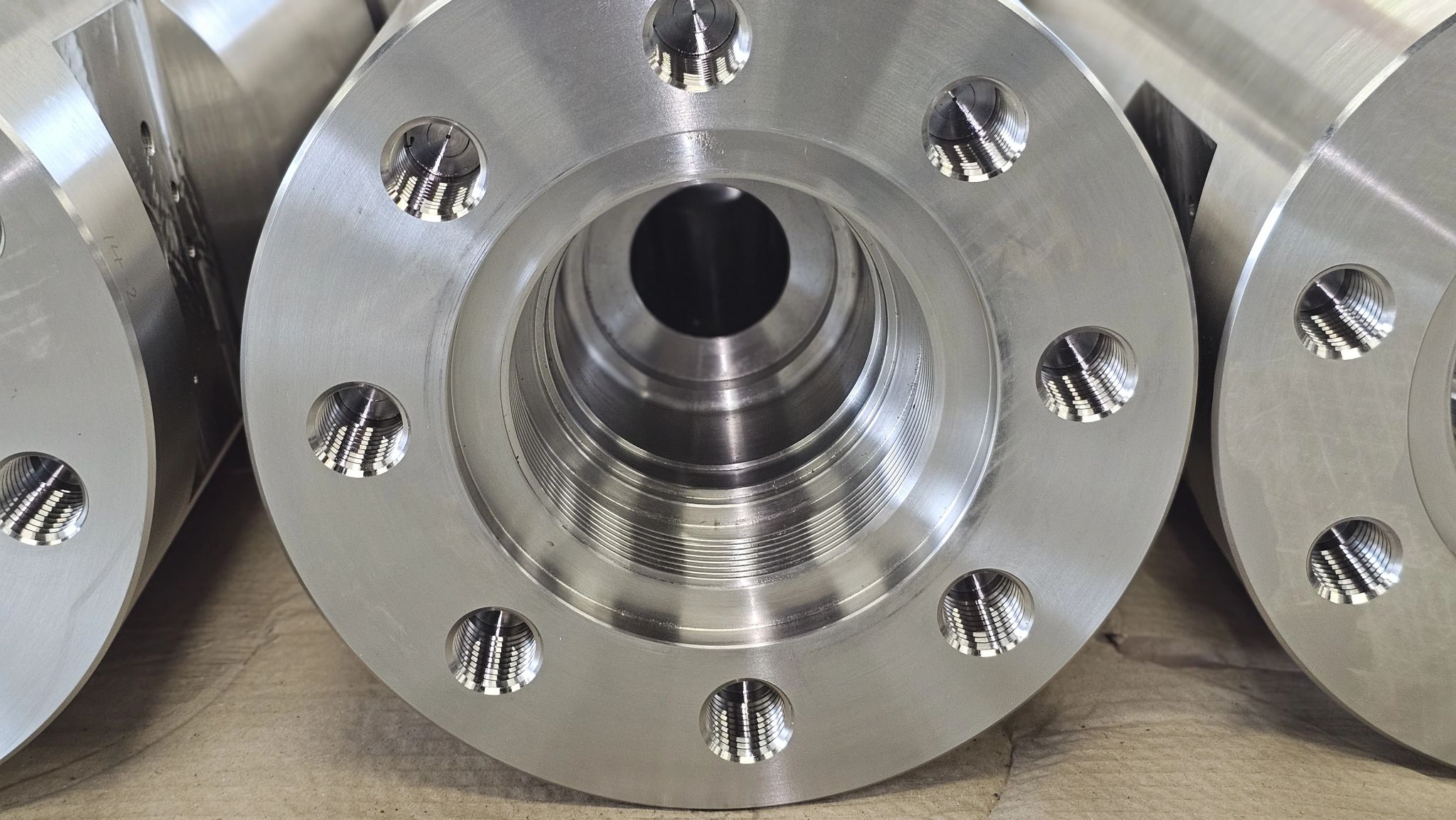
Precision Manufacturing: Turning and Milling Techniques for Steel Connectors
The manufacturing process is pivotal in determining the accuracy and performance of valve body connectors used in fluid control systems. We utilize advanced turning and milling techniques, which combine the benefits of both methods to achieve superior precision in component fabrication.
This composite manufacturing process allows us to control critical dimensions rigorously, ensuring that each connector fits perfectly with its corresponding parts within the fluid control system. By employing state-of-the-art machinery and skilled operators, we can achieve tight tolerances that enhance the overall reliability of these connectors.
The refined surface quality obtained through these processes minimizes friction and wear, contributing to the durability of the connectors under high-pressure conditions typical in many fluid management applications. Furthermore, these techniques enable us to produce complex geometries that meet specific requirements for various uses—from petrochemical processing to water treatment solutions—ensuring optimal performance metrics across all applications.
Performance Metrics: Ensuring Reliability Under Pressure in Fluid Control Systems
When it comes to valve performance metrics, our focus is on ensuring that valve body connectors can withstand extreme conditions without compromising functionality within fluid control systems. The use of C45 steel enhances their ability to handle high pressures while maintaining structural integrity.
We evaluate performance through rigorous testing, assessing factors such as tensile strength, corrosion resistance, and fatigue life. These metrics are crucial for applications where failure is not an option, such as in pharmaceutical fluid control or energy sectors. By prioritizing these performance standards, we can confidently assert that our valve body connectors will deliver reliable service over extended periods, thus optimizing operational efficiency across various industries reliant on effective fluid management solutions.
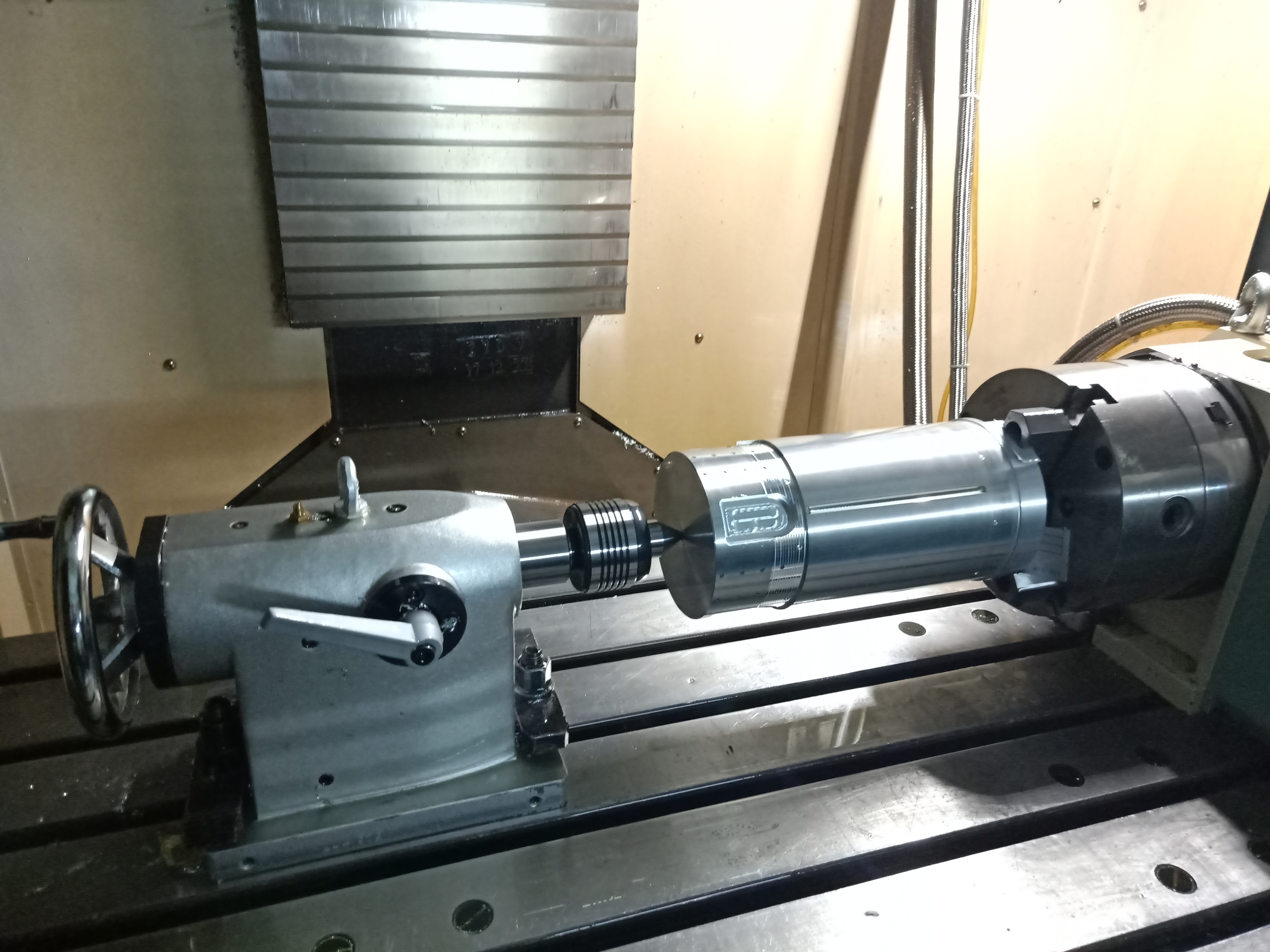
Applications of Valve Body Connectors in Fluid Control
Valve body connectors are integral components across numerous sectors, showcasing their versatility in fluid control systems. In industries like petrochemicals, they facilitate the safe transport of volatile substances under high pressure while ensuring reliable operation.
Their role in water treatment solutions ensures effective management of resources while adhering to environmental regulations critical for sustainable practices. In pharmaceuticals, these connectors maintain sterile conditions during fluid transfer processes, contributing significantly to product safety and compliance with stringent industry standards.Additionally, in automated industrial systems, valve body connectors enhance operational efficiency by enabling seamless integration with various control mechanisms essential for effective fluid management. The adaptability of these connectors extends beyond traditional uses; they can be customized for specific applications through innovative design approaches and advanced manufacturing techniques.
This flexibility makes them an essential choice for engineers and manufacturers looking to optimize performance across diverse operational landscapes reliant on precise fluid control solutions.
Challenges and Innovations in Valve Manufacturing for Fluid Control Applications
Despite their many advantages, we face challenges in valve manufacturing that require innovative solutions within the realm of fluid control. Issues such as material fatigue under extreme conditions or corrosion over time necessitate ongoing research and development.
We are continuously exploring new materials and coatings that enhance the durability and reliability of valve body connectors while maintaining cost-effectiveness crucial for competitive markets. Innovations such as advanced surface treatments or composite materials may provide additional protection against environmental stresses faced by these components.
Moreover, integrating smart technologies into valve design can lead to enhanced monitoring capabilities within fluid control systems, allowing for real-time assessments of connector performance. By addressing these challenges through innovation, we ensure that our products remain at the forefront of technology while meeting the evolving demands of various industries dependent on efficient fluid management solutions.
Future Trends in Valve Body Connectors Within Fluid Control Systems
Despite their many advantages, we face challenges in valve manufacturing that require innovative solutions within the realm of fluid control. Issues such as material fatigue under extreme conditions or corrosion over time necessitate ongoing research and development.
Looking ahead, we anticipate significant advancements in valve body connector technology driven by trends such as automation and sustainability within fluid control frameworks. As industries increasingly adopt automated processes, the demand for highly reliable and efficient valve systems will continue to grow. We expect developments in smart materials that respond dynamically to environmental changes or operational demands will emerge as a key focus area within fluid management solutions. Additionally, sustainability initiatives may drive innovations aimed at reducing waste during manufacturing processes or enhancing recyclability at the end of a product's life cycle.
Furthermore, as industries strive for greater efficiency in their operations, we foresee an increasing emphasis on precision engineering techniques that minimize tolerances and maximize performance metrics across all applications—ensuring that our valve body connectors remain essential components in modern industrial operations focused on effective fluid control.