Custom Bike Parts – Precision Crafted with CNC Technology
Custom Bike Parts CNC Machining Services
Get Quote and Start Your Project TodayISO 9001 Certified | 17+ Years CNC Machined Parts Experience
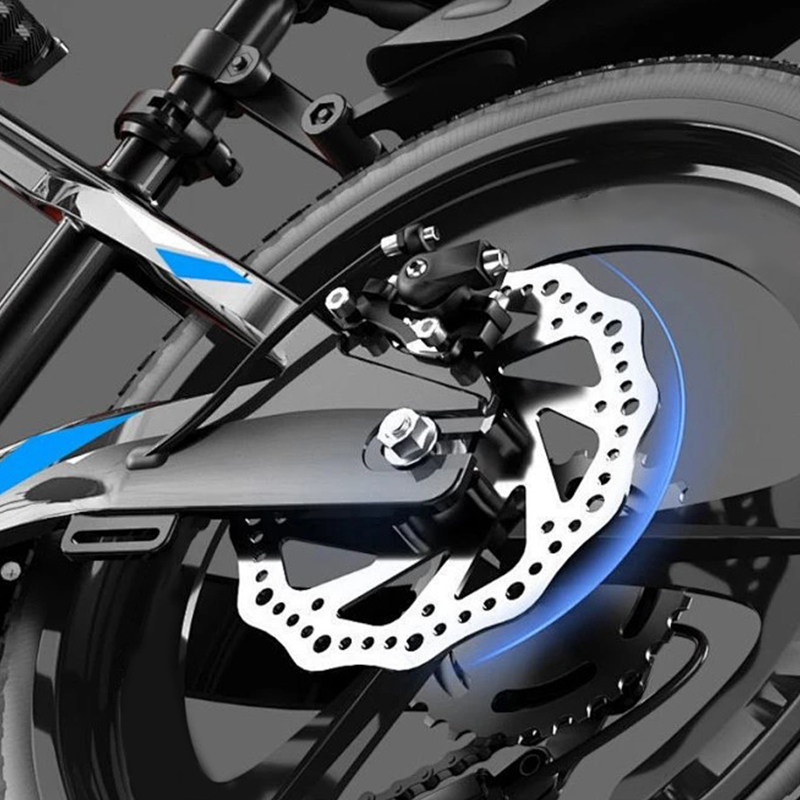
CNC technology has revolutionized the manufacturing of custom bicycle parts, offering unprecedented precision, efficiency, and customization options for cyclists and manufacturers alike. From intricate engine components to personalized handlebars and foot pegs, CNC machining enables the creation of high-quality, bespoke bike parts that enhance both performance and aesthetics.
Custom Bike Parts
Explore our comprehensive catalog spanning 8 categories and 50+ SKUs, including:-
•
Frames: Carbon fiber, titanium & steel options
-
•
Drivetrain Components: Custom chainrings & derailleur hangers
-
•
Wheelsets: Aerodynamic spokes & hub adapters
-
•
Handlebars: Ergonomic designs for endurance/racing
Custom Bicycle Pedals – Where Engineering Meets Art
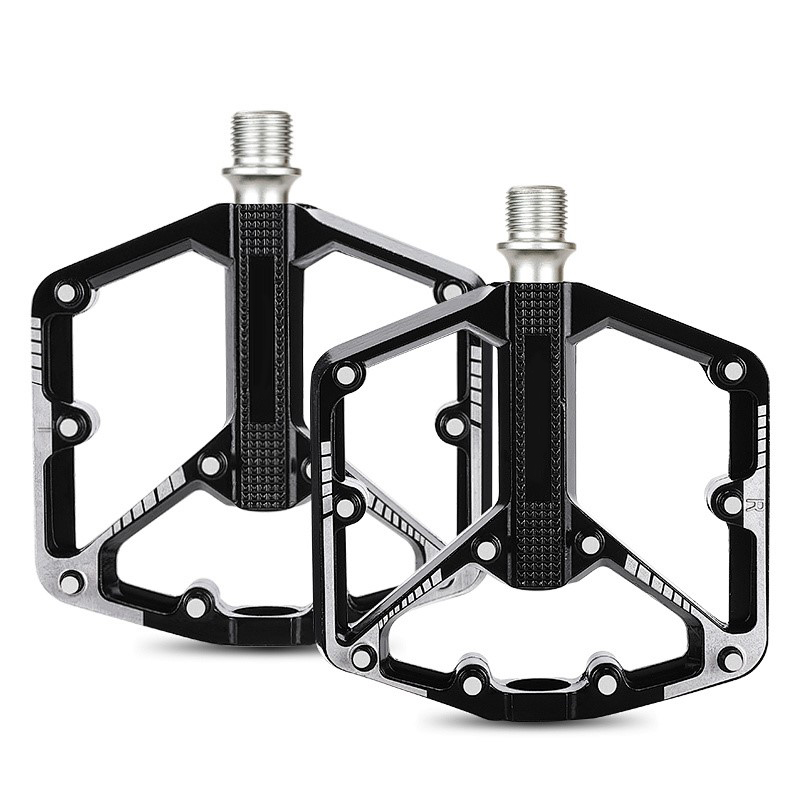
Our proprietary CNC process delivers:
-
✓
3D-milled traction patterns(6 patent-pending designs)
-
✓
Weight optimization Components 15% lighter vs. cast pedals
-
✓
Material flexibility Choose from 6061-T6 aluminum or grade 5 titanium
Ideal for gravel cyclists needing mud-shedding efficiency and downhill riders prioritizing grip.
Custom E-Bike Frame – Future-Proof Your Ride
Our proprietary CNC process delivers:
-
•
Integrated battery cavities with IP67-rated sealing
-
•
Stiffness-to-weight ratio 18% improvement over OEM designs
-
•
Smart cable routing Compatible with Bosch/Yamaha mid-drives
Includes finite element analysis (FEA) reports validating 10,000+ cycle durability.
CNC Milling for Bike Frames
CNC milling has become a game-changer in bicycle frame manufacturing, offering unparalleled precision and design flexibility. This advanced technique allows for the creation of fully machined frames from billet aluminum, significantly reducing the supply chain complexity compared to traditional welded frames.
The process involves using computer-controlled cutting tools to shape the frame components with extreme accuracy, resulting in perfectly aligned bearing interfaces and integrated cable management systems.
Key advantages of CNC milling for bike frames include:
-
•
Reduced manufacturing steps and lower minimum order quantities
-
•
Ability to create complex geometries and custom designs
-
•
Direct machining of bearing interfaces for improved alignment and performance
-
•
Seamless integration of features like cable routing and component mounts
-
•
Direct machining of bearing interfaces for improved alignment and performance
These benefits make CNC milling an attractive option for both small-scale custom builders and larger manufacturers seeking to produce high-performance, precisely engineered bicycle frames.
Precision CNC Turning Techniques
Precision CNC turning is a crucial technique in manufacturing custom bicycle parts, offering high accuracy and consistency for cylindrical components. This process involves rotating the workpiece while a cutting tool moves linearly to shape the material.
Technique | Application in Bicycle Manufacturing |
---|---|
CNC Lathe Turning | Crafting axially symmetrical parts like hubs and sprockets |
Multi-Axis Turning | Creating complex geometries for custom frame components |
Swiss-Type Turning | Producing small, precise parts for bicycle mechanisms |
CNC turning excels in producing shafts, a common element in bicycle design, and can work with various materials including aluminum, titanium, and steel. The precision of this technique allows for the creation of intricate details and shapes, enhancing both the functionality and aesthetics of custom bicycle parts.
Anodized Bicycle Parts – Durability Redefined
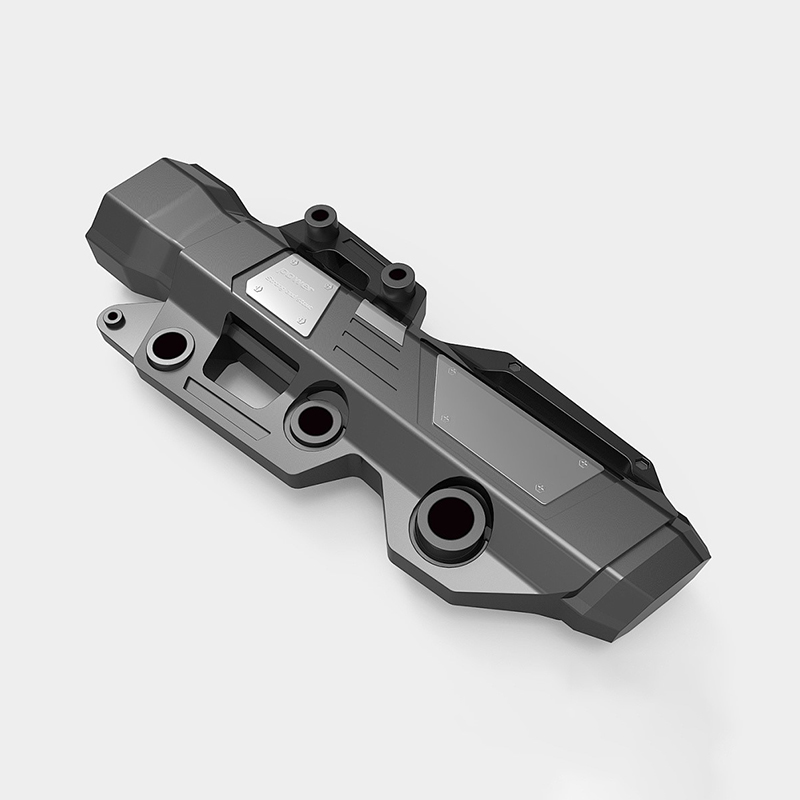
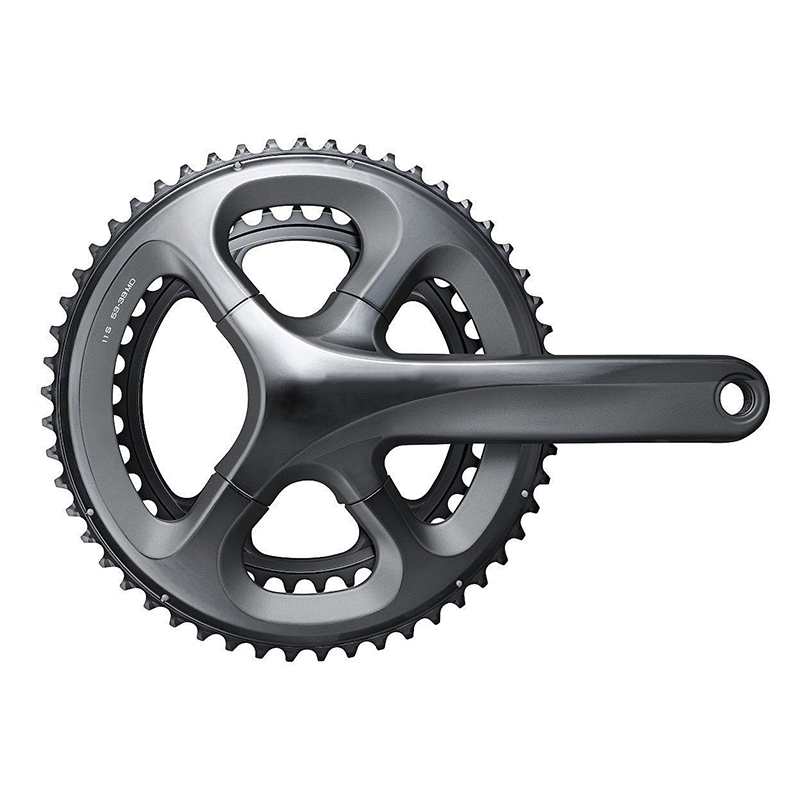
Our proprietary CNC process delivers:
-
◆
50μm oxide layer – 3x thicker than industry standard
-
◆
600+ color options via electrolytic pigmentation
-
◆
Corrosion resistance Passes 1000hr salt spray testing
Customizable Materials for Bike Parts
Custom bicycle parts can be manufactured using a variety of materials, each offering unique properties suited for different applications. Here's a quick overview of the most common materials used in custom bike part production:
Material | Key Properties | Common Applications |
---|---|---|
Aluminum | Lightweight, corrosion-resistant, affordable | Frames, rims, handlebars, pedals |
Steel | Strong, durable, comfortable ride | Frames, forks, cranks |
Titanium | Lightweight, strong, corrosion-resistant | High-end frames, bolts, brackets |
Carbon Fiber | Extremely lightweight, stiff, customizable | Frames, forks, handlebars, seat posts |
Each material offers distinct advantages for custom bike parts. Aluminum is popular for its versatility and cost-effectiveness, while steel provides durability and a smooth ride. Titanium combines strength with light weight, making it ideal for premium components. Carbon fiber, though more complex to machine, allows for precise tuning of ride characteristics and is favored for high-performance applications.
Bicycle Custom Frame – Bespoke Performance
Tailored for elite athletes and boutique builders:
-
•
Dynamic fitting sessions 20+ body metrics analyzed
-
•
Modular dropout system QR/Thru-axle convertible
-
•
Crash replacement program 30% discount on frame repairs
Custom Aluminum Bicycle Frame – The Weight Warrior
6061/7075 alloy frames featuring:
-
✓
Hydroformed tubesets: 18% weight reduction
-
✓
Internal reinforcement ribs: Eliminates flex under 300lb loads
-
✓
Custom etching: Add team logos or inspirational quotes
Dirt Jumper Parts – Built for Impact
Professional-grade components for slopestyle/park riding:
-
•
4mm chromoly chain tensioners
-
•
Oversized pivot bearings (15mm ID)
-
•
Gusset-reinforced stems: 25° rise options
Custom Hardtail MTB – Trail Dominance
Optimized for technical singletrack:
-
◆
Asymmetric chainstays : 142mm Boost spacing
-
◆
Tapered head tubes: 44mm/56mm options
-
◆
Removable rack mounts : Stealth integration