Thread Forming vs Thread Cutting Fasteners: Complete Guide to Self-Tapping Screws
Thread-forming fasteners, a type of self-tapping screw, are engineered to create threads by displacing material rather than cutting it, offering robust and stress-resistant joints across various substrates.
Widely used in industries like electronics, automotive, and construction, these fasteners excel in applications involving plastics, metals, and other materials, providing efficient solutions without the need for pre-drilling while ensuring optimal performance through precise design and material-specific considerations.
Widely used in industries like electronics, automotive, and construction, these fasteners excel in applications involving plastics, metals, and other materials, providing efficient solutions without the need for pre-drilling while ensuring optimal performance through precise design and material-specific considerations.
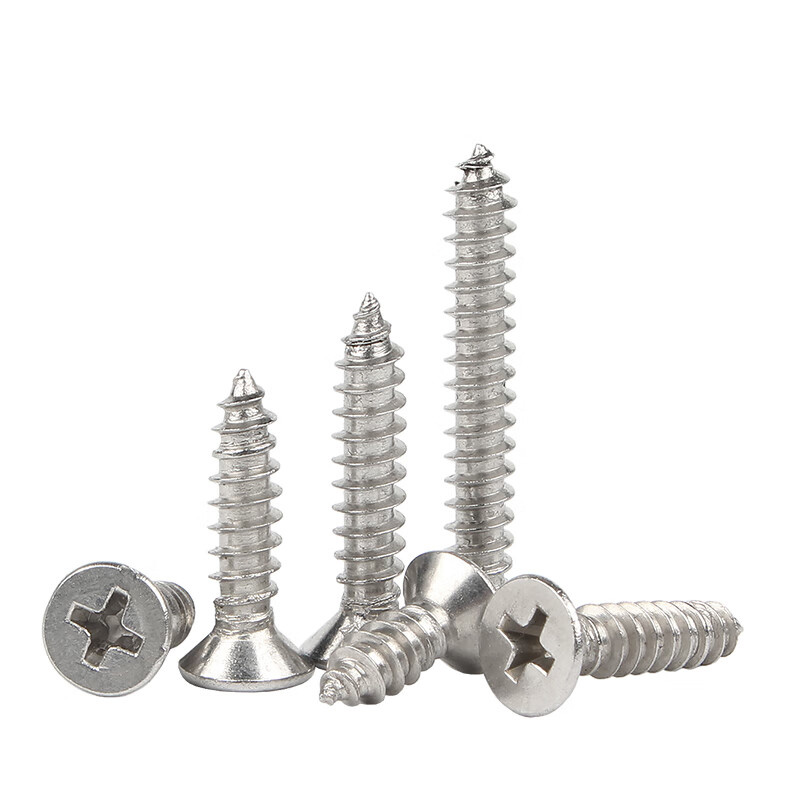
Self-tapping screws
Basic Principles of Thread Forming
Thread forming is a dynamic process that relies on the plastic deformation of the substrate material. The basic principle involves displacing material rather than removing it, creating a stronger joint with increased fatigue resistance.The process begins when the screw is driven into an unthreaded pilot hole, with the screw's special geometry initiating material deformation into the mating thread configuration.
The thread forming process can be characterized by a torque-time curve with distinct phases:
-
•
Initial torque spike (Thread Forming Torque)
-
•
Gradual increase due to Thread Friction Torque
-
•
Sharp rise at screw head seating (Driving Torque)
-
•
Final increase to failure point
Material Deformation Process
The material deformation process during thread forming is characterized by complex plastic flow patterns that vary depending on the substrate properties. In thermoplastics, the thread-forming screw induces localized heating, causing the material to flow around the screw threads and create a zero-clearance fit. This process results in higher internal stresses compared to thread-cutting screws, but also provides superior resistance to loosening.For metals, the deformation behavior differs significantly. The thread-forming process in metals involves cold working, where the material is displaced and work-hardened around the screw threads. This results in increased fatigue resistance and improved pull-out strength compared to pre-tapped holes. The deformation process is highly sensitive to temperature, with elevated temperatures generally facilitating easier material flow but potentially compromising the final joint strength. In contrast, colder temperatures can increase the required insertion torque and may lead to material cracking, especially in brittle substrates.
Types of Thread Forming Fasteners
Self-tapping screws create their own threads by displacing or removing material. Their smaller thread profile angle reduces radial stresses during deformation, enabling better thread engagement and holding power in soft materials.Thread-Forming vs Thread-Cutting Screws
Thread-forming and thread-cutting screws are two distinct types of self-tapping fasteners, each with unique characteristics suited for specific applications. The following table summarizes their key differences:Characteristic | Thread-Forming Screws | Thread-Cutting Screws |
---|---|---|
Material Interaction | Displace material | Remove material |
Pilot Hole | May not require | Typically require |
Torque for Insertion | Higher | Lower |
Stress on Material | Higher internal stresses | Lower internal stresses |
Loosening Resistance | Higher | Lower |
Typical Applications | High-performance thermoplastics, sheet metal | Wood, metal, harder materials |
Reusability | Often reusable | Limited reusability |
In contrast, thread-cutting screws are ideal for harder materials or when lower insertion torque is needed. They create mating threads by removing material, resulting in a more precise fit but potentially lower holding power.
Thread-Forming vs Conventional Fasteners
Self-tapping screws offer distinct advantages over ordinary screws, particularly in applications requiring efficient installation and secure fastening. The following table compares key characteristics of self-tapping and ordinary screws:Characteristic | Self-Tapping Screws | Ordinary Screws |
---|---|---|
Thread Formation | Create own threads | Require pre-tapped holes |
Pilot Hole | May not require or smaller | Typically require |
Installation Speed | Faster | Slower |
Material Compatibility | Versatile (metal, wood, plastic) | Limited by pre-tapping |
Holding Power | Generally stronger | Varies based on tapping |
Reusability | Often reusable | Typically reusable |
Specialized Types | Self-drilling variants available | Limited specialization |
However, ordinary screws may be preferred in situations where precise thread matching is critical or when working with very hard materials that could damage self-tapping screws. The choice between self-tapping and ordinary screws ultimately depends on the specific application requirements, material properties, and installation efficiency needs.
Material-Specific Application Considerations
Self-tapping screws exhibit versatile applications across various materials, each requiring specific considerations:-
•
Metal: Ideal for sheet metal work, particularly in automotive, machinery, and furniture construction. For aluminum, use screws with drill-like points and sharp cutting blade threads to prevent denting.
-
•
Wood: Effective in softer woods, facilitating quick assembly of structures and furniture. Pre-drilling is recommended for thin wood to prevent splitting.
-
•
Plastic: Suitable for assembling plastic components, with thread-forming screws preferred for most thermoplastics to reduce stress and increase pull-out resistance.
-
•
Concrete: Specialized self-tapping screws are available for concrete applications.
For more demanding metal sheet applications, self-drilling screws offer enhanced functionality. These fasteners combine drilling and tapping capabilities, allowing them to penetrate and fasten light gauge sheet metal in a single operation without the need for pre-drilled pilot holes. This feature makes them particularly valuable in industries such as automotive and aviation, where one-sided access to thin metal components is often a challenge.
Common Metal Material Analysis
Self-tapping screws are commonly used with various metal materials, each requiring specific considerations for optimal performance:
-
•
Carbon Steel: Widely used for its strength and cost-effectiveness. Self-tapping screws for carbon steel often feature case-hardened surfaces to enhance durability and cutting ability
-
•
Dielectric fluid: Oil-based EDM can achieve Ra 0.2 μm, while water-based EDM reaches Ra 0.4 μm.
-
•
Stainless Steel: Preferred for corrosion resistance, particularly in marine or chemical environments. A2 (304) and A4 (316) grades are common, with A4 offering superior corrosion resistance.
-
•
Aluminum: Requires careful screw selection due to its softness. Self-drilling screws with sharp cutting edges are often preferred to prevent material deformation.
-
•
Sheet Metal: Type A self-tapping screws are suitable for thin sheets (0.015" to 0.05"), while Type B screws work better for thicker gauges (0.05" to 0.2").
Additionally, the screw's thread design and tip configuration should match the specific metal properties to ensure optimal thread formation and joint strength.
Applications in Plastic
Self-tapping screws designed for plastics offer unique advantages in various applications, particularly in industries like electronics, automotive, and consumer goods. These screws are specifically engineered to form threads in plastic materials without causing damage or stress cracking.
-
•
Thread-forming screws, such as PT® and Delta PT® screws, are preferred for plastics due to their 30° thread angle, which reduces radial stresses and improves material flow. The REMFORM® II™ screw features an asymmetrical thread design that minimizes radial hoop stress, making it ideal for a wide range of engineered plastics.
-
•
For thermoplastics with a flexural modulus of 150,000 to 400,000 psi, thread-forming screws are particularly effective. In softer plastics, these screws can achieve up to 10 disassembly and reassembly cycles, making them suitable for products requiring occasional maintenance.
-
•
When using self-tapping screws in plastics, it's crucial to consider the material's properties and choose the appropriate screw type. For instance, thermosetting plastics, being less ductile, may require thread-cutting screws instead of thread-forming variants.
Process Optimization Parameters
Pilot hole design is crucial for optimal self-tapping screw performance. The pilot hole diameter should typically be between the minor and major diameter of the screw thread. For example, a #6 screw may require a pilot hole of approximately 2.5-3.0 mm. Proper sizing prevents material splitting and ensures efficient thread formation.Torque control is essential for successful installation. The tightening torque (MA) should be at least 1.2 times the insertion torque (ME) but not exceed 0.5 times the stripping torque (MÜ). Using a high-torque, low-RPM drill with torque control settings is recommended. The optimal torque ratio (MÜ/ME) enhances connection reliability.
Common issues include:
-
•
Over-tightening, leading to stripped threads or material deformation
-
•
Incorrect screw size selection for the material thickness
-
•
Excessive drilling speed causing bit overheating and blunting
-
•
Improper placement, affecting structural integrity