EDM Machining: High-Precision Wire Cutting Solutions
The AccuteX GE Series Wire EDM machines stand out for their advanced features, including high-speed cutting, intelligent discharge capabilities, and structural innovations, making them ideal for applications in industries like aerospace, medical devices, and mold manufacturing.
EDM Machining Fundamentals
Electrical Discharge Machining (EDM) is a sophisticated metal-cutting process that utilizes controlled electrical sparks to precisely shape conductive materials. Unlike conventional machining methods, EDM employs thermal energy to erode the workpiece, allowing for the creation of complex geometries in hard materials with exceptional accuracyThe EDM process involves two main components: an electrode and a workpiece, both submerged in a dielectric fluid. When a high-voltage potential difference is applied between them, a series of rapid electrical discharges occur, generating temperatures between 8,000 and 12,000 degrees Celsius in the spark gap. This intense heat causes localized melting and vaporization of the workpiece material, which is then flushed away by the dielectric fluid.
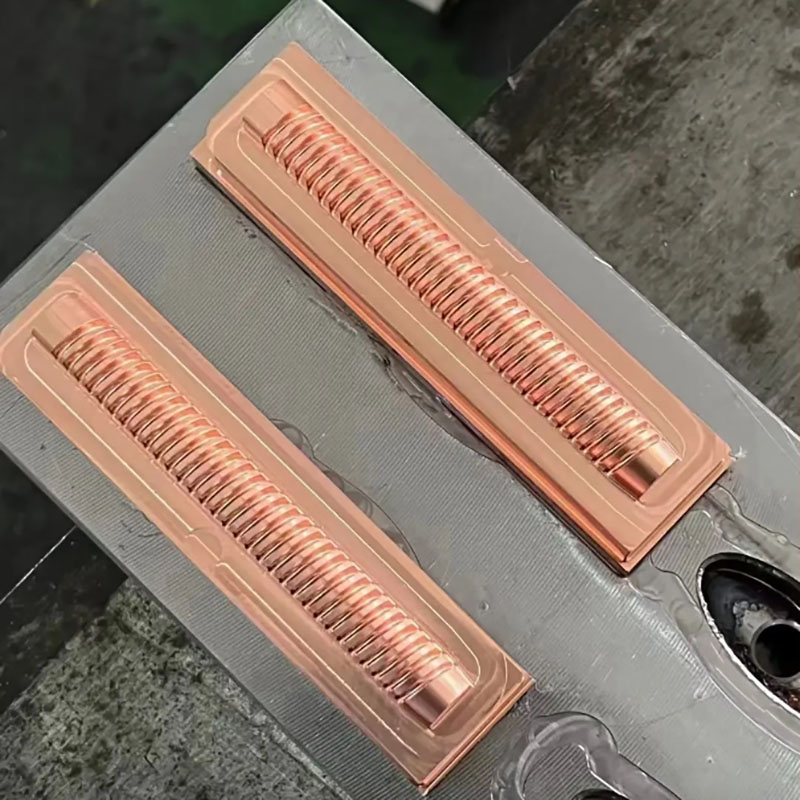
Thermo-Electrical Material Removal
The EDM machining process relies on controlled electrical discharges to erode conductive materials. In this process, an electrode (tool) and workpiece are submerged in a dielectric fluid and connected to opposite poles of a power supply. As the electrode approaches the workpiece, a spark gap of 0.05-0.25 mm is maintained. When voltage is applied, electrical breakdown occurs, creating a plasma channel that generates temperatures of 8,000-12,000°C.This intense heat melts and vaporizes small portions of the workpiece material, which are then flushed away by the dielectric fluid. The process repeats rapidly, with up to 10,000 sparks per second, gradually shaping the workpiece to the desired form. Key factors influencing the EDM process include:
-
•
Electrode material and shape
-
•
Dielectric fluid composition
-
•
Power supply parameters (voltage, current, frequency)
-
•
Spark gap distance
-
•
Flushing efficiency for debris removal
EDM Process Variants
Electrical Discharge Machining (EDM) encompasses several specialized techniques, each tailored to specific manufacturing needs. The following table outlines the primary types of EDM and their key characteristics: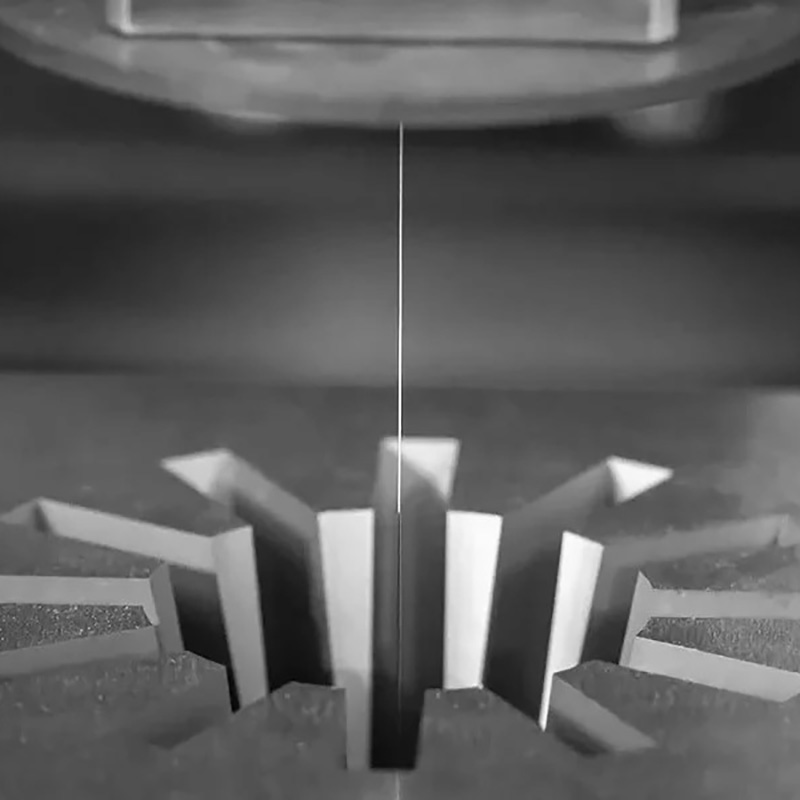
EDM Type | Description | Key Features |
---|---|---|
Die-sinking EDM | Uses a shaped electrode to create inverse cavities | - Ideal for complex 3D shapes- Employs graphite or copper electrodes- Suitable for sharp internal corners |
Wire EDM | Utilizes a thin, moving wire as the electrode | - Precision cutting of 2D shapes in 3D parts- Achieves tolerances as low as 0.0001 inches- Excellent for intricate details and fine cuts |
Hole-drilling EDM | Specialized for creating small, deep holes | - Efficient for high aspect ratio holes- Used in aerospace and automotive industries- Capable of producing holes as small as 0.1 mm in diameter |
Micro EDM | Focuses on extremely small-scale machining | - Uses electrodes as thin as 0.1 mm- Achieves features in the micrometer range- Critical for microelectronics and medical devices |
Each EDM type offers unique advantages for specific applications. Die-sinking EDM excels in creating complex molds and dies, while Wire EDM is preferred for cutting precise profiles and intricate shapes. Hole-drilling EDM is crucial for creating cooling channels in turbine blades and fuel injector nozzles. Micro EDM has found increasing use in miniaturized components for various high-tech industries.
The choice of EDM type depends on factors such as desired geometry, material properties, and required precision. For instance, aerospace components often require a combination of Wire EDM for external profiles and Die-sinking EDM for internal features. The medical industry leverages Wire EDM for manufacturing surgical instruments and implants, benefiting from its ability to work with biocompatible materials like titanium.
Recent advancements in EDM technology have led to hybrid machines that combine multiple EDM types or integrate EDM with conventional machining processes, further expanding the capabilities and efficiency of this versatile manufacturing technique.
Wire EDM for Intricate Shapes
Wire EDM excels in creating intricate shapes and complex geometries, making it ideal for precision components in industries like aerospace and medical device manufacturing. The process utilizes a thin, electrically charged wire (typically 0.1-0.3 mm in diameter) to cut through conductive materials with extreme accuracy, achieving tolerances as tight as 0.0001 inches.Modern wire EDM machines support multi-axis control and ultra-thin wires (as small as 0.0012 inches), enabling the production of highly detailed 3D components with features like tight corners, fine details, and angled surfaces. This capability, combined with the absence of physical contact between the cutting tool and workpiece, allows for the machining of delicate or weak materials without distortion, making wire EDM particularly valuable for creating complex molds, dies, and precision parts that would be challenging or impossible to produce using traditional machining methods.
GE Series Wire Cutting Machines
The GE Series Wire Cutting Machines from AccuteX represent a pinnacle in wire EDM technology, offering superior cost-performance ratios and cutting speeds that outpace competitors.These machines feature a unique structural design where the Y-axis is located on the base and the X-axis is positioned atop it, optimizing precision for small to medium stroke mold cutting operations. The series incorporates advanced features such as:
-
•
SD MASTER (Standard) technology for enhanced machining repeatability
-
•
Direct motor drive in X/Y axes for high servo response
-
•
Finite Element Analysis (FEA) designed structure for optimal rigidity
-
•
Intelligent discharge unit capable of adapting to varying workpiece thicknesses and water flushing conditions
-
•
Wire consumption offset functionality to compensate for wire thinning during thick workpiece cutting
DM Surface Finish Capabilities
EDM can achieve exceptionally fine surface finishes, with roughness values (Ra) typically ranging from 0.2 to 0.8 μm. The surface quality depends on several factors:-
•
Machining parameters: Lower discharge energy, shorter pulse durations, and higher frequencies yield finer finishes
-
•
Dielectric fluid: Oil-based EDM can achieve Ra 0.2 μm, while water-based EDM reaches Ra 0.4 μm
-
•
Material properties: Denser materials generally allow smoother finishes with fewer passes
-
•
Post-processing: Multiple skim cuts can further improve surface quality
EDM Pros and Cons
EDM offers unique advantages in precision manufacturing, particularly for complex geometries in hard, conductive materials. Its non-contact nature allows for machining delicate parts without distortion, achieving tolerances as tight as ±0.005 inches.EDM excels in creating intricate shapes and fine details, making it invaluable for aerospace and medical device industries. However, EDM has significant limitations. It's restricted to electrically conductive materials, excluding plastics and ceramics.
The process is relatively slow compared to conventional machining, with lower material removal rates. EDM also incurs high operational costs due to energy consumption, electrode wear, and the need for specialized dielectric fluids. Additionally, the thermal nature of the process can induce surface alterations, potentially requiring post-processing
-
•
Pros: High precision, ability to machine hard materials, no physical contact
-
•
Cons: Limited to conductive materials, slow processing speed, high operational costs
Optimal EDM Application Scenarios
EDM is particularly advantageous when conventional machining methods are inadequate or impractical. It excels in creating complex geometries, tight tolerances, and fine details in electrically conductive materials, especially hard alloys. Key applications include: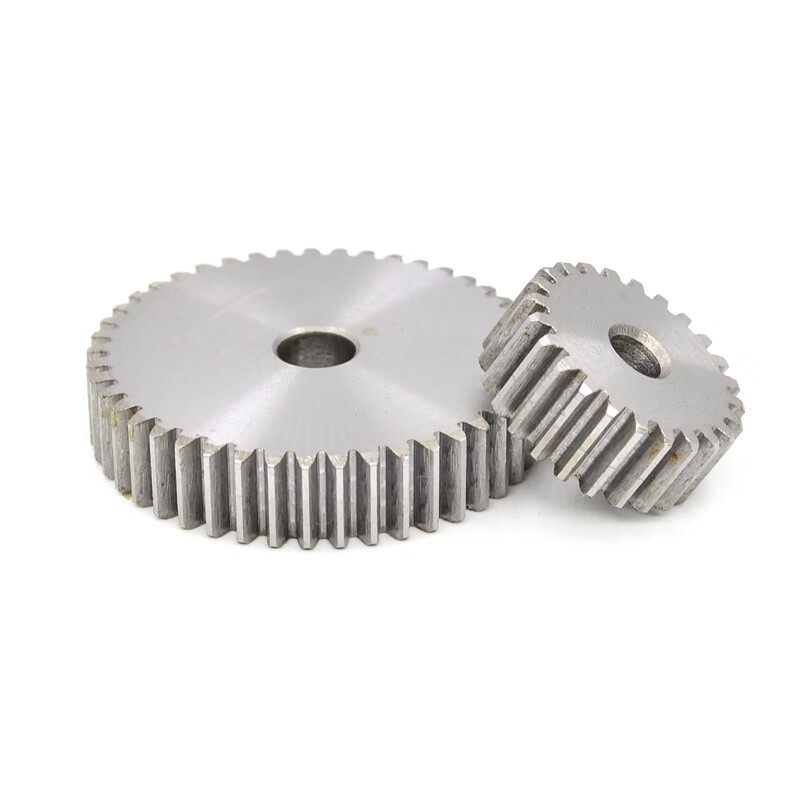
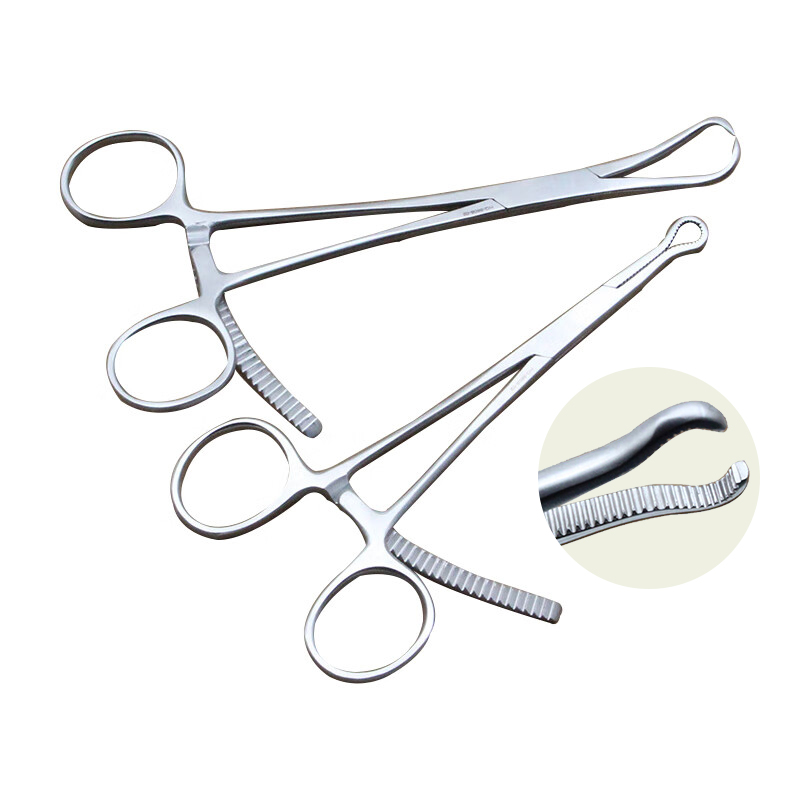
-
•
Producing sharp internal corners and intricate shapes in molds and dies
-
•
Manufacturing aerospace components with high-precision requirements
-
•
Drilling micro-holes or curved holes in automotive and medical parts
-
•
Cutting extrusions and rotary forms with minimal material waste
-
•
Removing broken tools or fasteners from workpieces
-
•
Machining thin-walled or small parts prone to distortion under mechanical forces
-
What materials can be cut with Wire EDM?
Any electrically conductive material can be machined, including hardened steels, titanium, Incone, and carbides. However, it's not cost-effective for soft materials like copper or brass, which are better suited for conventional machining.
-
What's the maximum material thickness for Wire EDM?
Advanced machines can cut materials up to 15.75" thick while maintaining precision. This capability allows for the production of large, complex parts in a single setup.
-
How accurate is Wire EDM?
Modern Wire EDM machines can achieve positioning and contour accuracy of ±2 microns (0.00008"). This extreme precision makes Wire EDM ideal for applications requiring tight tolerances.
-
What surface finish can be achieved?
With multiple cutting passes, Wire EDM can produce surface finishes as fine as Ra 0.08μm. This eliminates the need for additional finishing operations in many cases.
-
Can Wire EDM cut multiple parts simultaneously?