Thread Milling vs Tapping: How to Choose for Materials up to 65 HRC
When selecting a threading method for CNC machining, the choice between thread milling and tapping hinges on material hardness, production scale, and cost efficiency. This guide dives into critical factors like tool durability, precision, and machining costs, with a focus on hard materials up to 65 HRC (Rockwell Hardness Scale, a standard for measuring material hardness).
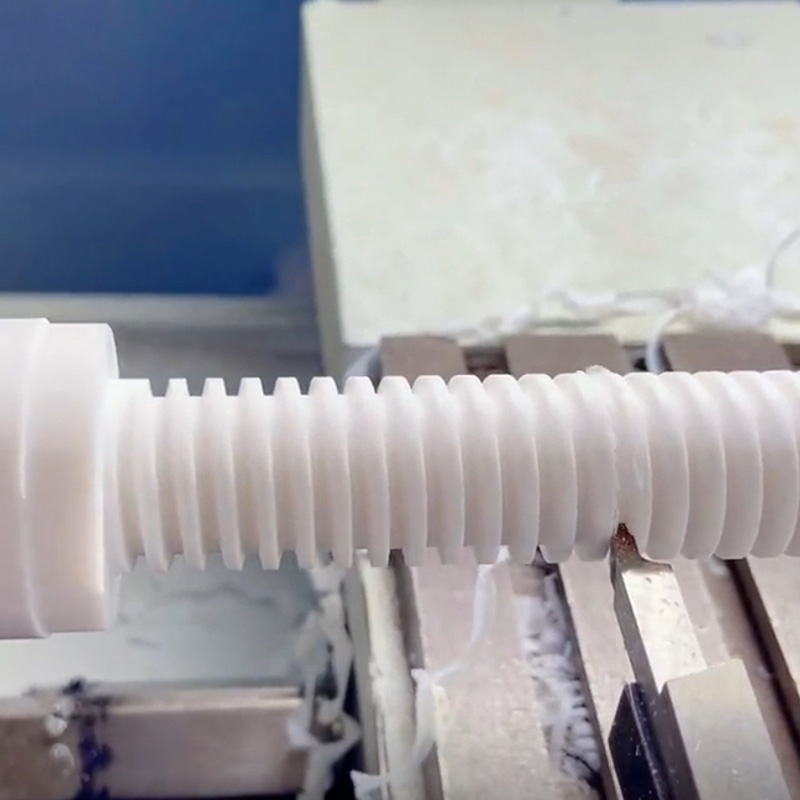
Key Technical Comparison Table
Thread milling and tapping are two distinct methods for creating threads, each with its own set of characteristics and applications. The following table summarizes the key differences between these two processes:Aspect | Thread Milling | Tapping |
---|---|---|
Tool Durability | 500-800 holes in 60 HRC steel | 50-100 holes in 60 HRC steel |
HRC Range* | Up to 70 HRC | Max 45 HRC |
Cost per Thread (45 HRC) | $0.18 | $0.35 |
Chip Formation | Small, easily evacuated | Can be long and stringy |
Chip Management | Fragmented chips (1-3mm) | Continuous chips (10-30cm) |
Tool Durability in High-Hardness Machining
CNC thread milling for hard materials (>45 HRC) significantly outperforms tapping in tool life:
-
•
Data from Sandvik Coromant: Carbide thread mills last 3–5x longer than taps in 60–65 HRC steels (e.g., D2 tool steel).
-
Cost Impact: While a single thread mill costs 150-300 vs. 20-80 for a tap, the reduced replacement frequency lowers long-term costs by ~40% for batches over 500 units.
-
•
Standard HSS taps wear rapidly above 50 HRC, with failure rates exceeding 60% in 65 HRC materials due to torsional stress.
Precision & Chip Management
-
•
Thread Milling: Achieves IT7-IT8 tolerances (ISO standard for thread accuracy) even in hardened steels. Spiral chip evacuation reduces re-cutting risks.
-
Tapping: Limited to IT8-IT10 in hard materials. Chip accumulation in deep holes (>3xD) increases breakage risks by 35% (MSC Industrial Supply study).
Thread Milling for Hard Materials (>45 HRC)
Materials up to 65 HRC machining require specialized approaches. Thread milling excels here through:-
Technical Advantages:
-
•
Variable helix tools reduce harmonic vibration
-
•
High-pressure coolant (1000psi+) prevents work hardening
-
•
Trochoidal tool paths maintain 0.05mm chip thickness
-
•
-
Process Parameters for 55-65 HRC:
Parameter | Value |
---|---|
Cutting Speed | 25-35 m/min |
Feed per Tooth | 0.04-0.06 mm |
Stepover | 30% of tool diameter |
Coolant Pressure | Minimum 70 bar |
-
•
Speed: 60–100 SFM (surface feet per minute) for 60–65 HRC steels.
-
Depth of Cut: 0.5–1.5x thread pitch.
Case Study 1: Medical implant manufacturer reduced threading costs by 40% when switching to thread milling for 58 HRC stainless steel components.
Case Study 2: A turbine blade manufacturer reduced threading costs by 28% by switching to thread milling for Inconel 718 (45 HRC).
FAQ: Critical Manufacturing Questions
Q: Can you tap 65 HRC material? A: Conventional tapping becomes impractical above 45 HRC. At 65 HRC:-
•
Tap failure rate exceeds 80%
-
•
Thread quality (ISO 4g tolerance) unattainable
-
•
CNC thread milling hard materials is the viable solution, achieving ISO 2g tolerances consistently