Description
The mill-turn composite parts are manufactured by combining the machining processes of turning and milling. This method allows multiple machining steps to be completed on a single piece of equipment, thereby improving production efficiency and reducing processing time. Mill-turn composite parts typically feature complex geometries and high precision machining requirements, making them suitable for producing parts such as shafts, housings, and cylindrical components that demand precise dimensions and surface quality. Chi Heng Hardware Co., Ltd. is committed to providing high-quality mill-turn composite parts for the CNC machining industry to meet the diverse needs of customers in various application scenarios.
In modern manufacturing, mill-turn composite machining technology is highly regarded for its efficiency, precision, and versatility. Chi Heng Hardware Co., Ltd. adheres to the mission of providing customers with high-quality machining solutions, continuously innovating and enhancing the level of technology and services in mill-turn composite machining, and making a positive contribution to the development of the CNC machining industry.
I. Advantages of Mill-Turn Composite Machining
Mill-turn composite machining technology integrates the traditional machining processes of turning and milling on a single CNC machine. Compared to conventional single-process machining methods, mill-turn composite machining has the following significant advantages:
Increased Machining Efficiency: By completing multiple processes in one clamping operation, the time spent on transporting and clamping workpieces between different machines is reduced. This not only significantly shortens production cycles but also minimizes the possibility of human error.
High Precision Machining: Since mill-turn composite machining can complete various processes on the same machine, the positioning accuracy of the workpiece is greatly enhanced. This is particularly beneficial when machining complex parts, as mill-turn technology ensures high precision in the alignment of various machining surfaces, avoiding errors caused by repeated positioning.
Complex Shape Machining: Mill-turn composite machining is ideal for parts with complex shapes and multiple surfaces. Through programmed control, the machine can flexibly switch between turning and milling processes, easily meeting the machining requirements of various irregular surfaces, inclined planes, and helical grooves.
Cost Reduction: By reducing the transfer of workpieces between different processes, mill-turn composite machining effectively lowers production costs. Combined with the reduction in machining time and the improvement in precision, companies can produce higher-quality products with fewer resources and in less time.
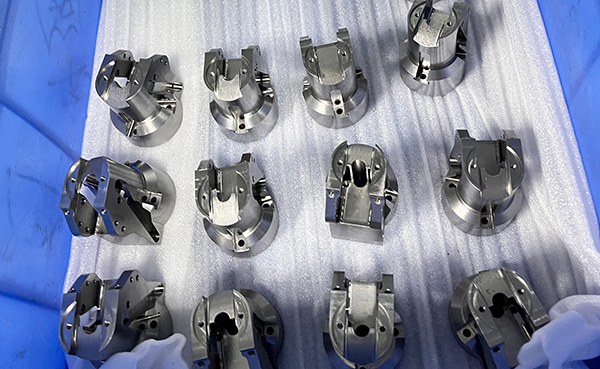
II. Application Fields of Mill-Turn Composite Parts
Mill-turn composite parts are widely used in high-precision manufacturing fields such as aerospace, automotive manufacturing, medical devices, and electronic communications. These fields demand extremely high levels of complexity and precision in parts, and mill-turn technology is the ideal choice to meet these stringent requirements.
For example, in the aerospace industry, engine parts are often complex in shape and made of hard materials, making it challenging for traditional machining processes to efficiently achieve the required precision. Mill-turn composite technology not only enables the machining of complex three-dimensional surfaces but also ensures the stability and reliability of parts under high-temperature and high-pressure conditions.
In the automotive manufacturing field, mill-turn composite parts are widely used in the machining of key components such as engines, transmissions, and chassis. These components require extremely high dimensional accuracy and surface finish, and even slight deviations can affect the overall performance of the vehicle. Mill-turn composite machining technology can meet these stringent requirements while significantly improving production efficiency.
III. Chi Heng Hardware's Technological Advantages
Chi Heng Hardware Co., Ltd. possesses advanced mill-turn composite machining equipment and an experienced technical team. By introducing leading CNC equipment and machining processes from both domestic and international sources, we continuously optimize production processes to ensure the delivery of high-quality mill-turn composite parts to our customers.
Moreover, we emphasize personalized customization services, allowing us to flexibly adjust machining processes based on customers' specific needs to produce high-precision parts tailored to particular application scenarios. We understand that the needs of each industry and customer are unique, so Chi Heng Hardware is dedicated to providing tailored solutions to help customers enhance their product competitiveness.
Mill-turn composite parts, as a crucial component of modern manufacturing, play a vital role in various high-tech fields due to their efficiency, precision, and versatility. Chi Heng Hardware Co., Ltd. will continue to uphold the spirit of innovation and excellence, constantly improving mill-turn composite machining technology, and providing customers with superior products and services, contributing to the flourishing development of global manufacturing.
Dongguan Chiheng Hardwrare Co.,Ltd is a professional OEM metal fabrication factory which is located in Chang'an, Dongguan, China,and specialize in this field since 2009.
Our main business are CNC machining, plastic injection molding, die casting ,extrusion,Investment Casting and stamping parts.
We now have sophisticated CNC machining centers, engraving and drilling machine, Injection molding machine, stamping machine, compressor, lathe and milling machine, line cutting and other equipment.
With these machines and experienced employees, we are able to make repeated positioning accuracy within tolerance 0.005mm, providing strong guarantee for precision parts.
With great Service and nice quality,our products have been exported to USA, South America, Europe, Australia, Middle east and Southeast Asia, etc.Our goal is to make every customer happy.